Поликарбонаты — Википедия
Структурная формула поликарбоната — эфира бисфенола АПоликарбонаты — группа термопластов, сложные полиэфиры угольной кислоты и двухатомных спиртов общей формулы (-O-R-O-CO-)n. Наибольшее промышленное значение имеют ароматические поликарбонаты, в первую очередь, поликарбонат на основе Бисфенола А, благодаря доступности бисфенола А, синтезируемого конденсацией фенола и ацетона.
История возникновения
Первые упоминания о продукте, подобном поликарбонату, появились в XIX веке. В 1898 году получение поликарбоната впервые описал немецкий химик, изобретатель новокаина Альфред Эйнхорн. Тогда он работал у знаменитого химика-органика Адольфа фон Байера в Мюнхене и, занимаясь поиском обезболивающего средства из эфира, произвел в лаборатории реакции хлорангидрида угольной кислоты с тремя изомерами диоксибензола и в осадке получил полимерный эфир угольной кислоты — прозрачное, нерастворимое и термостойкое вещество.
В 1953 году Герман Шнелл, специалист немецкой компании «BAYER», получил соединение поликарбоната. Этот полимеризированный карбонат оказался соединением, механические свойства которого не имели аналогов среди известных термопластов. В том же году поликарбонат запатентовали под маркой «Макролон».
Но в этом же 1953 году, всего несколькими днями позже, поликарбонат получил Дениель Фокс, специалист из известной американской компании «General Electric». Возникла спорная ситуация. В 1955 году её удалось решить, и компания «General Electric» запатентовала материал под маркой поликарбонат «Лексан». В 1958 году «BAYER», а затем в 1960 году «General Electric» пустили в промышленное производство технически пригодный поликарбонат. В дальнейшем права на «Лексан» были проданы компании «Sabic» (Саудовская Аравия).
Но это было всего лишь вещество-поликарбонат. До появления сотового (или ячеистого) поликарбоната как листового материала оставалось еще долгих 20 лет.
В начале 1970-х годов в поисках альтернативы тяжёлому и хрупкому стеклу поликарбонатом заинтересовался Израиль, правительство которого активно поддерживало развитие сельского хозяйства и животноводчества в условиях жаркой пустыни. В частности, большое внимание уделялось теплицам, позволяющим выращивать растения в микроклимате, созданном с помощью капельного орошения. Стекло для изготовления теплиц было дорого и непрочно, акрил не мог удержать соответствующую температуру, а поликарбонат идеально для этого подходил.
Тогда совместно «General Electric» (владельцами сырья поликарбоната торговой марки «Лексан») проводились опыты по производству прозрачных пластиковых изделий на оборудовании компании «Polygal» в Рамат Ха-Шофете и Мегиддо (Израиль). Обе компании подгоняли технологию под сырьё, а сырьё — под технологию. Так, в Израиле в 1976 году получили первый в мире сотовый лист из поликарбоната
Методы синтеза
Синтез поликарбоната на основе бисфенола А проводится двумя методами: методом фосгенирования бисфенола А и методом переэтерификации в расплаве диарилкарбонатов бисфенолом А.
В случае переэтерификации в расплаве в качестве исходного сырья используется дифенилкарбонат, реакцию проводят в присутствии щелочных катализаторов (метилат натрия), температуру реакционной смеси повышают ступенчато от 150 до 300 °C, реакцию проводят в вакуумированных реакторах периодического действия при постоянной отгонке выделяющегося в ходе реакции фенола. Полученный расплав поликарбоната охлаждают и гранулируют. Недостатком метода является относительно небольшая молекулярная масса (до 50 КДа) получаемого полимера и его загрязнённость остатками катализатора и продуктов термодеструкции бисфенола А.
Фосгенирование бисфенола А проводят в растворе хлоралканов (обычно хлористого метилена CH2Cl2) при комнатной температуре, существует две модификации процесса — поликонденсация в растворе и межфазная поликонденсация:
При поликонденсации в растворе в качестве катализатора и основания, связывающего выделяющийся хлороводород используют пиридин, гидрохлорид пиридина, образующийся в ходе реакции, нерастворим в хлористом метилене и по завершении реакции его отделяют фильтрованием. От остаточных количеств пиридина, содержащегося в реакционной смеси, избавляются отмыванием водным раствором кислоты. Поликарбонат высаждают из раствора подходящим кислородсодержащим растворителем (ацетоном и т. п.), что позволяет частично избавиться от остаточных количеств бисфенола А, осадок сушат и гранулируют. Недостатком метода является использование достаточно дорогого пиридина в больших количествах (более 2 молей на моль фосгена).
В случае фосгенирования в условиях межфазного катализа поликонденсация проводится в два этапа: сначала фосгенированием бисфенолята А натрия получают раствор смеси олигомеров, которые содержат концевые хлорформиатные -OCOCl и гидроксильные -OH группы, после чего проводят поликонденсацию смеси олигомеров в полимер.
Переработка
При переработке поликарбонатов применяют большинство методов переработки и формовки термопластичных полимеров: литьё под давлением (производство изделий), выдувное литьё (разного рода сосуды), экструзию (производство профилей и плёнок), формовку волокон из расплава. При производстве поликарбонатных плёнок также применяется формовка из растворов — этот метод позволяет получать тонкие плёнки из поликарбонатов высокой молекулярной массы, формовка тонких плёнок из которых затруднена вследствие их высокой вязкости. В качестве растворителя обычно используют метиленхлорид.
Мировое производство
Поликарбонаты являются крупнотоннажными продуктами органического синтеза, мировые производственные мощности в 2006 года составляли более 3 млн тонн в год. Основные производители поликарбоната (2006)[1]:
Производитель | Объём производства | Торговые марки |
---|---|---|
Bayer Material Science AG | 900 000 т/год | Makrolon, Apec, Bayblend, Makroblend[2] |
900 000 т/год | Lexan | |
Samyang Busines Chemicals | 360 000 т/год | Trirex[3] |
Dow Chemical / LG DOW Polycarbonate | 300 000 т/год | Calibre[4] |
Teijin | 300 000 т/год | Panlite[5] |
Всего | 3 200 000 т/год |
Применение
Благодаря сочетанию высоких механических и оптических качеств монолитный пластик также применяется в качестве материала при изготовлении линз, компакт-дисков, фар, компьютеров[уточнить], очков и светотехнических изделий. Наиболее популярный в России формат применения — листовой поликарбонат: ячеистый («
Благодаря высокой прочности и ударной вязкости (250—500 кдж/м2) применяются в качестве конструкционных материалов в различных отраслях промышленности, используются при изготовлении защитных шлемов для экстремальных дисциплин вело- и мотоспорта. При этом для улучшения механических свойств применяются и наполненные стекловолокном композиции.
Стандартный поликарбонат не подходит для применений с длительным воздействием УФ-излучения. При этом происходит изменение оптических (помутнение, пожелтение) и механических (становится хрупким) свойств материала. Чтобы избежать этого, первичная смола может содержать УФ-стабилизаторы. Эти марки продаются как УФ-стабилизированный поликарбонат для литьевых и экструзионных компаний. Также поликарбонатные листы могут содержать анти-УФ-слой в качестве специального покрытия для повышения устойчивости к атмосферным воздействиям.
Поликарбонат был выбран в качестве материала для производства прозрачных вставок в медалях Зимних Олимпийских игр 2014 в Сочи, главным образом из-за его большого коэффициента теплового расширения, а также ввиду прочности, пластичности, удобства нанесения рисунка лазером[6].
Теплица остеклённая листовым монолитным матовым поликарбонатом
Лист сотового поликарбоната толщиной 6 мм
Теплица из неокрашенного (бесцветного) сотового поликарбоната
Золотая олимпийская медаль Зимних Олимпийских игр 2014 года в Сочи
Размеры и масса сотового поликарбоната
Размеры поликарбоната
Номинальная ширина стандартных панелей поликарбоната согласно ГОСТ Р 56712-2015 составляют 2100 мм. Номинальная длина: 6000 мм и 12000 мм. Однако в продаже чаще всего встречаются следующие типоразмеры (данные в формате: ширина х длина х толщина, мм):
- сотового:
- 2100 х 12000 х от 4 до 25;
- 2100 х 6000 х от 4 до 25;
- монолитного:
- 2050 х 1250 х 1
- 2050 х 3050 х от 1,5 до 12
Масса поликарбоната
Масса сотового поликарбоната чаще всего измеряется для квадратного метра определённой толщины[7]. Согласно ГОСТ Р 56712-2015 масса составляет:
- толщина: 4 мм, масса квадратного метра: 0,8 кг;
- толщина: 6 мм, масса квадратного метра: 1,3 кг;
- толщина: 8 мм, масса квадратного метра: 1,5 кг;
- толщина: 10 мм, масса квадратного метра: 1,7 кг.
См. также
Примечания
Литература
- ГОСТ 25288-82 «Пластмассы конструкционные. Номенклатура показателей».
- ГОСТ Р 51136-2008 «Стёкла защитные многослойные. Общие технические условия».
Поликарбонаты — Википедия
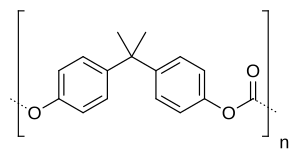
Поликарбонаты — группа термопластов, сложные полиэфиры угольной кислоты и двухатомных спиртов общей формулы (-O-R-O-CO-)n. Наибольшее промышленное значение имеют ароматические поликарбонаты, в первую очередь, поликарбонат на основе Бисфенола А, благодаря доступности бисфенола А, синтезируемого конденсацией фенола и ацетона.
История возникновения
Первые упоминания о продукте, подобном поликарбонату, появились в XIX веке. В 1898 году получение поликарбоната впервые описал немецкий химик, изобретатель новокаина Альфред Эйнхорн. Тогда он работал у знаменитого химика-органика Адольфа фон Байера в Мюнхене и, занимаясь поиском обезболивающего средства из эфира, произвел в лаборатории реакции хлорангидрида угольной кислоты с тремя изомерами диоксибензола и в осадке получил полимерный эфир угольной кислоты — прозрачное, нерастворимое и термостойкое вещество.
В 1953 году Герман Шнелл, специалист немецкой компании «BAYER», получил соединение поликарбоната. Этот полимеризированный карбонат оказался соединением, механические свойства которого не имели аналогов среди известных термопластов. В том же году поликарбонат запатентовали под маркой «Макролон».
Но в этом же 1953 году, всего несколькими днями позже, поликарбонат получил Дениель Фокс, специалист из известной американской компании «General Electric». Возникла спорная ситуация. В 1955 году её удалось решить, и компания «General Electric» запатентовала материал под маркой поликарбонат «Лексан». В 1958 году «BAYER», а затем в 1960 году «General Electric» пустили в промышленное производство технически пригодный поликарбонат. В дальнейшем права на «Лексан» были проданы компании «Sabic» (Саудовская Аравия).
Но это было всего лишь вещество-поликарбонат. До появления сотового (или ячеистого) поликарбоната как листового материала оставалось еще долгих 20 лет.
В начале 1970-х годов в поисках альтернативы тяжёлому и хрупкому стеклу поликарбонатом заинтересовался Израиль, правительство которого активно поддерживало развитие сельского хозяйства и животноводчества в условиях жаркой пустыни. В частности, большое внимание уделялось теплицам, позволяющим выращивать растения в микроклимате, созданном с помощью капельного орошения. Стекло для изготовления теплиц было дорого и непрочно, акрил не мог удержать соответствующую температуру, а поликарбонат идеально для этого подходил.
Тогда совместно «General Electric» (владельцами сырья поликарбоната торговой марки «Лексан») проводились опыты по производству прозрачных пластиковых изделий на оборудовании компании «Polygal» в Рамат Ха-Шофете и Мегиддо (Израиль). Обе компании подгоняли технологию под сырьё, а сырьё — под технологию. Так, в Израиле в 1976 году получили первый в мире сотовый лист из поликарбоната[источник не указан 716 дней].
Видео по теме
Методы синтеза
Синтез поликарбоната на основе бисфенола А проводится двумя методами: методом фосгенирования бисфенола А и методом переэтерификации в расплаве диарилкарбонатов бисфенолом А.
В случае переэтерификации в расплаве в качестве исходного сырья используется дифенилкарбонат, реакцию проводят в присутствии щелочных катализаторов (метилат натрия), температуру реакционной смеси повышают ступенчато от 150 до 300 °C, реакцию проводят в вакуумированных реакторах периодического действия при постоянной отгонке выделяющегося в ходе реакции фенола. Полученный расплав поликарбоната охлаждают и гранулируют. Недостатком метода является относительно небольшая молекулярная масса (до 50 КДа) получаемого полимера и его загрязнённость остатками катализатора и продуктов термодеструкции бисфенола А.
Фосгенирование бисфенола А проводят в растворе хлоралканов (обычно хлористого метилена CH2Cl2) при комнатной температуре, существует две модификации процесса — поликонденсация в растворе и межфазная поликонденсация:
При поликонденсации в растворе в качестве катализатора и основания, связывающего выделяющийся хлороводород используют пиридин, гидрохлорид пиридина, образующийся в ходе реакции, нерастворим в хлористом метилене и по завершении реакции его отделяют фильтрованием. От остаточных количеств пиридина, содержащегося в реакционной смеси, избавляются отмыванием водным раствором кислоты. Поликарбонат высаждают из раствора подходящим кислородсодержащим растворителем (ацетоном и т. п.), что позволяет частично избавиться от остаточных количеств бисфенола А, осадок сушат и гранулируют. Недостатком метода является использование достаточно дорогого пиридина в больших количествах (более 2 молей на моль фосгена).
В случае фосгенирования в условиях межфазного катализа поликонденсация проводится в два этапа: сначала фосгенированием бисфенолята А натрия получают раствор смеси олигомеров, которые содержат концевые хлорформиатные -OCOCl и гидроксильные -OH группы, после чего проводят поликонденсацию смеси олигомеров в полимер.
Переработка
При переработке поликарбонатов применяют большинство методов переработки и формовки термопластичных полимеров: литьё под давлением (производство изделий), выдувное литьё (разного рода сосуды), экструзию (производство профилей и плёнок), формовку волокон из расплава. При производстве поликарбонатных плёнок также применяется формовка из растворов — этот метод позволяет получать тонкие плёнки из поликарбонатов высокой молекулярной массы, формовка тонких плёнок из которых затруднена вследствие их высокой вязкости. В качестве растворителя обычно используют метиленхлорид.
Мировое производство
Поликарбонаты являются крупнотоннажными продуктами органического синтеза, мировые производственные мощности в 2006 года составляли более 3 млн тонн в год. Основные производители поликарбоната (2006)[1]:
Производитель | Объём производства | Торговые марки |
---|---|---|
Bayer Material Science AG | 900 000 т/год | Makrolon, Apec, Bayblend, Makroblend[2] |
Sabic Innovative Plastics | 900 000 т/год | Lexan |
Samyang Busines Chemicals | 360 000 т/год | Trirex[3] |
Dow Chemical / LG DOW Polycarbonate | 300 000 т/год | Calibre[4] |
Teijin | 300 000 т/год | Panlite[5] |
Всего | 3 200 000 т/год |
Применение
Благодаря сочетанию высоких механических и оптических качеств монолитный пластик также применяется в качестве материала при изготовлении линз, компакт-дисков, фар, компьютеров, очков и светотехнических изделий. Наиболее популярный в России формат применения — листовой поликарбонат: ячеистый («сотовый поликарбонат» или замковые панели сотового поликарбоната) и сплошной (монолитный поликарбонат). Листовой поликарбонат применяется в качестве светопрозрачного материала в строительстве. Также материал используется там, где требуется повышенная теплоустойчивость. Это могут быть светопрозрачные вставки в кровлю и фасадные конструкции, теплицы, навесы, шумовые ограждения дорог и так далее. Разнообразность применения листового поликарбоната связана с уникальным комплексом свойств: прозрачность, легкость, прочность, гибкость, долговечность (при наличии УФ защитного слоя). В мае 2015 года утвержден ГОСТ Р 56712-2015 «Панели многослойные из поликарбоната». Монолитный поликарбонат сертифицируется по ГОСТ Р 51136 «Защитные стекла».
Благодаря высокой прочности и ударной вязкости (250—500 кдж/м2) применяются в качестве конструкционных материалов в различных отраслях промышленности, используются при изготовлении защитных шлемов для экстремальных дисциплин вело- и мотоспорта. При этом для улучшения механических свойств применяются и наполненные стекловолокном композиции.
Стандартный поликарбонат не подходит для применений с длительным воздействием УФ-излучения. При этом происходит изменение оптических (помутнение, пожелтение) и механических (становится хрупким) свойств материала. Чтобы избежать этого, первичная смола может содержать УФ-стабилизаторы. Эти марки продаются как УФ-стабилизированный поликарбонат для литьевых и экструзионных компаний. Также поликарбонатные листы могут содержать анти-УФ-слой в качестве специального покрытия для повышения устойчивости к атмосферным воздействиям.
Поликарбонат был выбран в качестве материала для производства прозрачных вставок в медалях Зимних Олимпийских игр 2014 в Сочи, главным образом из-за его большого коэффициента теплового расширения, а также ввиду прочности, пластичности, удобства нанесения рисунка лазером[6].
Размеры и масса сотового поликарбоната
Размеры поликарбоната
Номинальная ширина стандартных панелей поликарбоната согласно ГОСТ Р 56712-2015 составляют 2100 мм. Номинальная длина: 6000 мм и 12000 мм. Однако в продаже чаще всего встречаются следующие типоразмеры (данные в формате: ширина х длина х толщина, мм):
- 2100 х 12000 х от 4 до 25;
- 2100 х 6000 х от 4 до 25.
Масса поликарбоната
Масса сотового поликарбоната чаще всего измеряется для квадратного метра определённой толщины[7]. Согласно ГОСТ Р 56712-2015 масса составляет:
- толщина: 4 мм, масса квадратного метра: 0,8 кг;
- толщина: 6 мм, масса квадратного метра: 1,3 кг;
- толщина: 8 мм, масса квадратного метра: 1,5 кг;
- толщина: 10 мм, масса квадратного метра: 1,7 кг.
См. также
Примечания
Сотовый поликарбонат Википедия
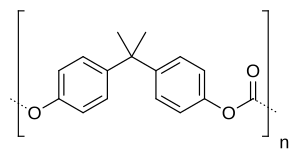
Поликарбонаты — группа термопластов, сложные полиэфиры угольной кислоты и двухатомных спиртов общей формулы (-O-R-O-CO-)n. Наибольшее промышленное значение имеют ароматические поликарбонаты, в первую очередь, поликарбонат на основе Бисфенола А, благодаря доступности бисфенола А, синтезируемого конденсацией фенола и ацетона.
История возникновения[ | ]
Первые упоминания о продукте, подобном поликарбонату, появились в XIX веке. В 1898 году получение поликарбоната впервые описал немецкий химик, изобретатель новокаина Альфред Эйнхорн. Тогда он работал у знаменитого химика-органика Адольфа фон Байера в Мюнхене и, занимаясь поиском обезболивающего средства из эфира, произвёл в лаборатории реакции хлорангидрида угольной кислоты с тремя изомерами диоксибензола и в осадке получил полимерный эфир угольной кислоты — прозрачное, нерастворимое и термостойкое вещество.
В 1953 году Герман Шнелл, специалист немецкой компании «BAYER», получил соединение поликарбоната. Этот полимеризированный карбонат оказался соединением, механические свойства которого не имели аналогов среди известных термопластов. В том же году поликарбонат запатентовали под маркой «Макролон».
Но в этом же 1953 году, всего несколькими днями позже, поликарбонат получил Дениель Фокс, специалист из известной американской компании «General Electric». Возникла спорная ситуация. В 1955 году её удалось решить, и компания «General Electric» запатентовала материал под маркой поликарбонат «Лексан». В 1958 году «BAYER», а затем в 1960 году «General Electric» пустили в промышленное производство технически пригодный поликарбонат. В дальнейшем права на «Лексан» были проданы компании «Sabic» (Саудовская Аравия).
Но это было всего лишь вещество-поликарбонат. До появления сотового (или ячеистого) поликарбоната как листового материала оставалось ещё долгих 20 лет.
В начале 1970-х годов в поисках альтернативы тяжёлому и хрупкому стеклу поликарбонатом заинтересовался Израиль, правительство которого активно поддерживало развитие сельского хозяйства и животноводчества в условиях жаркой пустыни. В частности, большое внимание уделялось теплицам, позволяющим выращивать растения в микроклимате, созданном с помощью капельного орошения. Стекло для изготовления теплиц было дорого и непрочно, акрил не мог удержать соответствующую температуру, а поликарбонат идеально для этого подходил.
Тогда совместно «General Electric» (владельцами сырья поликарбоната торговой марки «Лексан») проводились опыты по производству прозрачных пластиковых изделий на оборудовании компании «Polygal» в Рамат Ха-Шофете и Мегиддо (Израиль). Обе компании подгоняли технологию под сырьё, а сырьё — под технологию. Так, в Израиле в 1976 году получили первый в мире сотовый лист из поликарбоната[источник не указан 1160 дней].
Методы синтеза[ | ]
Синтез поликарбоната на основе бисфенола А проводится двумя методами: методом фосгенирования бисфенола А и методом переэтерификации в расплаве диарилкарбонатов бисфенолом А.
В случае переэтерификации в расплаве в качестве исходного сырья используется дифенилкарбонат, реакцию проводят в присутствии щелочных катализаторов (метилат натрия), температуру реакционной смеси повышают ступенчато от 150 до 300 °C, реакцию проводят в вакуумированных реакторах периодического действия при постоянной отгонке выделяющегося в ходе реакции фенола. Полученный расплав поликарбоната охлаждают и гранулируют. Недостатком метода является относительно небольшая молекулярная масса (до 50 КДа) получаемого полимера и его загрязнённость остатками катализатора и продуктов термодеструкции бисфенола А.
Фосгенирование бисфенола А проводят в растворе хлоралканов (обычно хлористого метилена CH2Cl2) при комнатной температуре, су
Поликарбонаты — Википедия. Что такое Поликарбонаты
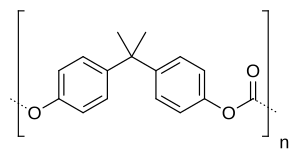
Поликарбонаты — группа термопластов, сложные полиэфиры угольной кислоты и двухатомных спиртов общей формулы (-O-R-O-CO-)n. Наибольшее промышленное значение имеют ароматические поликарбонаты, в первую очередь, поликарбонат на основе Бисфенола А, благодаря доступности бисфенола А, синтезируемого конденсацией фенола и ацетона.
История возникновения
Первые упоминания о продукте, подобном поликарбонату, появились в XIX веке. В 1898 году получение поликарбоната впервые описал немецкий химик, изобретатель новокаина Альфред Эйнхорн. Тогда он работал у знаменитого химика-органика Адольфа фон Байера в Мюнхене и, занимаясь поиском обезболивающего средства из эфира, произвел в лаборатории реакции хлорангидрида угольной кислоты с тремя изомерами диоксибензола и в осадке получил полимерный эфир угольной кислоты — прозрачное, нерастворимое и термостойкое вещество.
В 1953 году Герман Шнелл, специалист немецкой компании «BAYER», получил соединение поликарбоната. Этот полимеризированный карбонат оказался соединением, механические свойства которого не имели аналогов среди известных термопластов. В том же году поликарбонат запатентовали под маркой «Макролон».
Но в этом же 1953 году, всего несколькими днями позже, поликарбонат получил Дениель Фокс, специалист из известной американской компании «General Electric». Возникла спорная ситуация. В 1955 году её удалось решить, и компания «General Electric» запатентовала материал под маркой поликарбонат «Лексан». В 1958 году «BAYER», а затем в 1960 году «General Electric» пустили в промышленное производство технически пригодный поликарбонат. В дальнейшем права на «Лексан» были проданы компании «Sabic» (Саудовская Аравия).
Но это было всего лишь вещество-поликарбонат. До появления сотового (или ячеистого) поликарбоната как листового материала оставалось еще долгих 20 лет.
В начале 1970-х годов в поисках альтернативы тяжёлому и хрупкому стеклу поликарбонатом заинтересовался Израиль, правительство которого активно поддерживало развитие сельского хозяйства и животноводчества в условиях жаркой пустыни. В частности, большое внимание уделялось теплицам, позволяющим выращивать растения в микроклимате, созданном с помощью капельного орошения. Стекло для изготовления теплиц было дорого и непрочно, акрил не мог удержать соответствующую температуру, а поликарбонат идеально для этого подходил.
Тогда совместно «General Electric» (владельцами сырья поликарбоната торговой марки «Лексан») проводились опыты по производству прозрачных пластиковых изделий на оборудовании компании «Polygal» в Рамат Ха-Шофете и Мегиддо (Израиль). Обе компании подгоняли технологию под сырьё, а сырьё — под технологию. Так, в Израиле в 1976 году получили первый в мире сотовый лист из поликарбоната[источник не указан 716 дней].
Методы синтеза
Синтез поликарбоната на основе бисфенола А проводится двумя методами: методом фосгенирования бисфенола А и методом переэтерификации в расплаве диарилкарбонатов бисфенолом А.
В случае переэтерификации в расплаве в качестве исходного сырья используется дифенилкарбонат, реакцию проводят в присутствии щелочных катализаторов (метилат натрия), температуру реакционной смеси повышают ступенчато от 150 до 300 °C, реакцию проводят в вакуумированных реакторах периодического действия при постоянной отгонке выделяющегося в ходе реакции фенола. Полученный расплав поликарбоната охлаждают и гранулируют. Недостатком метода является относительно небольшая молекулярная масса (до 50 КДа) получаемого полимера и его загрязнённость остатками катализатора и продуктов термодеструкции бисфенола А.
Фосгенирование бисфенола А проводят в растворе хлоралканов (обычно хлористого метилена CH2Cl2) при комнатной температуре, существует две модификации процесса — поликонденсация в растворе и межфазная поликонденсация:
При поликонденсации в растворе в качестве катализатора и основания, связывающего выделяющийся хлороводород используют пиридин, гидрохлорид пиридина, образующийся в ходе реакции, нерастворим в хлористом метилене и по завершении реакции его отделяют фильтрованием. От остаточных количеств пиридина, содержащегося в реакционной смеси, избавляются отмыванием водным раствором кислоты. Поликарбонат высаждают из раствора подходящим кислородсодержащим растворителем (ацетоном и т. п.), что позволяет частично избавиться от остаточных количеств бисфенола А, осадок сушат и гранулируют. Недостатком метода является использование достаточно дорогого пиридина в больших количествах (более 2 молей на моль фосгена).
В случае фосгенирования в условиях межфазного катализа поликонденсация проводится в два этапа: сначала фосгенированием бисфенолята А натрия получают раствор смеси олигомеров, которые содержат концевые хлорформиатные -OCOCl и гидроксильные -OH группы, после чего проводят поликонденсацию смеси олигомеров в полимер.
Переработка
При переработке поликарбонатов применяют большинство методов переработки и формовки термопластичных полимеров: литьё под давлением (производство изделий), выдувное литьё (разного рода сосуды), экструзию (производство профилей и плёнок), формовку волокон из расплава. При производстве поликарбонатных плёнок также применяется формовка из растворов — этот метод позволяет получать тонкие плёнки из поликарбонатов высокой молекулярной массы, формовка тонких плёнок из которых затруднена вследствие их высокой вязкости. В качестве растворителя обычно используют метиленхлорид.
Мировое производство
Поликарбонаты являются крупнотоннажными продуктами органического синтеза, мировые производственные мощности в 2006 года составляли более 3 млн тонн в год. Основные производители поликарбоната (2006)[1]:
Производитель | Объём производства | Торговые марки |
---|---|---|
Bayer Material Science AG | 900 000 т/год | Makrolon, Apec, Bayblend, Makroblend[2] |
Sabic Innovative Plastics | 900 000 т/год | Lexan |
Samyang Busines Chemicals | 360 000 т/год | Trirex[3] |
Dow Chemical / LG DOW Polycarbonate | 300 000 т/год | Calibre[4] |
Teijin | 300 000 т/год | Panlite[5] |
Всего | 3 200 000 т/год |
Применение
Благодаря сочетанию высоких механических и оптических качеств монолитный пластик также применяется в качестве материала при изготовлении линз, компакт-дисков, фар, компьютеров, очков и светотехнических изделий. Наиболее популярный в России формат применения — листовой поликарбонат: ячеистый («сотовый поликарбонат» или замковые панели сотового поликарбоната) и сплошной (монолитный поликарбонат). Листовой поликарбонат применяется в качестве светопрозрачного материала в строительстве. Также материал используется там, где требуется повышенная теплоустойчивость. Это могут быть светопрозрачные вставки в кровлю и фасадные конструкции, теплицы, навесы, шумовые ограждения дорог и так далее. Разнообразность применения листового поликарбоната связана с уникальным комплексом свойств: прозрачность, легкость, прочность, гибкость, долговечность (при наличии УФ защитного слоя). В мае 2015 года утвержден ГОСТ Р 56712-2015 «Панели многослойные из поликарбоната». Монолитный поликарбонат сертифицируется по ГОСТ Р 51136 «Защитные стекла».
Благодаря высокой прочности и ударной вязкости (250—500 кдж/м2) применяются в качестве конструкционных материалов в различных отраслях промышленности, используются при изготовлении защитных шлемов для экстремальных дисциплин вело- и мотоспорта. При этом для улучшения механических свойств применяются и наполненные стекловолокном композиции.
Стандартный поликарбонат не подходит для применений с длительным воздействием УФ-излучения. При этом происходит изменение оптических (помутнение, пожелтение) и механических (становится хрупким) свойств материала. Чтобы избежать этого, первичная смола может содержать УФ-стабилизаторы. Эти марки продаются как УФ-стабилизированный поликарбонат для литьевых и экструзионных компаний. Также поликарбонатные листы могут содержать анти-УФ-слой в качестве специального покрытия для повышения устойчивости к атмосферным воздействиям.
Поликарбонат был выбран в качестве материала для производства прозрачных вставок в медалях Зимних Олимпийских игр 2014 в Сочи, главным образом из-за его большого коэффициента теплового расширения, а также ввиду прочности, пластичности, удобства нанесения рисунка лазером[6].
Размеры и масса сотового поликарбоната
Размеры поликарбоната
Номинальная ширина стандартных панелей поликарбоната согласно ГОСТ Р 56712-2015 составляют 2100 мм. Номинальная длина: 6000 мм и 12000 мм. Однако в продаже чаще всего встречаются следующие типоразмеры (данные в формате: ширина х длина х толщина, мм):
- 2100 х 12000 х от 4 до 25;
- 2100 х 6000 х от 4 до 25.
Масса поликарбоната
Масса сотового поликарбоната чаще всего измеряется для квадратного метра определённой толщины[7]. Согласно ГОСТ Р 56712-2015 масса составляет:
- толщина: 4 мм, масса квадратного метра: 0,8 кг;
- толщина: 6 мм, масса квадратного метра: 1,3 кг;
- толщина: 8 мм, масса квадратного метра: 1,5 кг;
- толщина: 10 мм, масса квадратного метра: 1,7 кг.
См. также
Примечания
Поликарбонаты — Википедия
Структурная формула поликарбоната — эфира бисфенола АПоликарбонаты — группа термопластов, сложные полиэфиры угольной кислоты и двухатомных спиртов общей формулы (-O-R-O-CO-)n. Наибольшее промышленное значение имеют ароматические поликарбонаты, в первую очередь, поликарбонат на основе Бисфенола А, благодаря доступности бисфенола А, синтезируемого конденсацией фенола и ацетона.
История возникновения
Первые упоминания о продукте, подобном поликарбонату, появились в XIX веке. В 1898 году получение поликарбоната впервые описал немецкий химик, изобретатель новокаина Альфред Эйнхорн. Тогда он работал у знаменитого химика-органика Адольфа фон Байера в Мюнхене и, занимаясь поиском обезболивающего средства из эфира, произвел в лаборатории реакции хлорангидрида угольной кислоты с тремя изомерами диоксибензола и в осадке получил полимерный эфир угольной кислоты — прозрачное, нерастворимое и термостойкое вещество.
В 1953 году Герман Шнелл, специалист немецкой компании «BAYER», получил соединение поликарбоната. Этот полимеризированный карбонат оказался соединением, механические свойства которого не имели аналогов среди известных термопластов. В том же году поликарбонат запатентовали под маркой «Макролон».
Но в этом же 1953 году, всего несколькими днями позже, поликарбонат получил Дениель Фокс, специалист из известной американской компании «General Electric». Возникла спорная ситуация. В 1955 году её удалось решить, и компания «General Electric» запатентовала материал под маркой поликарбонат «Лексан». В 1958 году «BAYER», а затем в 1960 году «General Electric» пустили в промышленное производство технически пригодный поликарбонат. В дальнейшем права на «Лексан» были проданы компании «Sabic» (Саудовская Аравия).
Но это было всего лишь вещество-поликарбонат. До появления сотового (или ячеистого) поликарбоната как листового материала оставалось еще долгих 20 лет.
В начале 1970-х годов в поисках альтернативы тяжёлому и хрупкому стеклу поликарбонатом заинтересовался Израиль, правительство которого активно поддерживало развитие сельского хозяйства и животноводчества в условиях жаркой пустыни. В частности, большое внимание уделялось теплицам, позволяющим выращивать растения в микроклимате, созданном с помощью капельного орошения. Стекло для изготовления теплиц было дорого и непрочно, акрил не мог удержать соответствующую температуру, а поликарбонат идеально для этого подходил.
Тогда совместно «General Electric» (владельцами сырья поликарбоната торговой марки «Лексан») проводились опыты по производству прозрачных пластиковых изделий на оборудовании компании «Polygal» в Рамат Ха-Шофете и Мегиддо (Израиль). Обе компании подгоняли технологию под сырьё, а сырьё — под технологию. Так, в Израиле в 1976 году получили первый в мире сотовый лист из поликарбоната[источник не указан 716 дней].
Методы синтеза
Синтез поликарбоната на основе бисфенола А проводится двумя методами: методом фосгенирования бисфенола А и методом переэтерификации в расплаве диарилкарбонатов бисфенолом А.
В случае переэтерификации в расплаве в качестве исходного сырья используется дифенилкарбонат, реакцию проводят в присутствии щелочных катализаторов (метилат натрия), температуру реакционной смеси повышают ступенчато от 150 до 300 °C, реакцию проводят в вакуумированных реакторах периодического действия при постоянной отгонке выделяющегося в ходе реакции фенола. Полученный расплав поликарбоната охлаждают и гранулируют. Недостатком метода является относительно небольшая молекулярная масса (до 50 КДа) получаемого полимера и его загрязнённость остатками катализатора и продуктов термодеструкции бисфенола А.
Фосгенирование бисфенола А проводят в растворе хлоралканов (обычно хлористого метилена CH2Cl2) при комнатной температуре, существует две модификации процесса — поликонденсация в растворе и межфазная поликонденсация:
При поликонденсации в растворе в качестве катализатора и основания, связывающего выделяющийся хлороводород используют пиридин, гидрохлорид пиридина, образующийся в ходе реакции, нерастворим в хлористом метилене и по завершении реакции его отделяют фильтрованием. От остаточных количеств пиридина, содержащегося в реакционной смеси, избавляются отмыванием водным раствором кислоты. Поликарбонат высаждают из раствора подходящим кислородсодержащим растворителем (ацетоном и т. п.), что позволяет частично избавиться от остаточных количеств бисфенола А, осадок сушат и гранулируют. Недостатком метода является использование достаточно дорогого пиридина в больших количествах (более 2 молей на моль фосгена).
В случае фосгенирования в условиях межфазного катализа поликонденсация проводится в два этапа: сначала фосгенированием бисфенолята А натрия получают раствор смеси олигомеров, которые содержат концевые хлорформиатные -OCOCl и гидроксильные -OH группы, после чего проводят поликонденсацию смеси олигомеров в полимер.
Переработка
При переработке поликарбонатов применяют большинство методов переработки и формовки термопластичных полимеров: литьё под давлением (производство изделий), выдувное литьё (разного рода сосуды), экструзию (производство профилей и плёнок), формовку волокон из расплава. При производстве поликарбонатных плёнок также применяется формовка из растворов — этот метод позволяет получать тонкие плёнки из поликарбонатов высокой молекулярной массы, формовка тонких плёнок из которых затруднена вследствие их высокой вязкости. В качестве растворителя обычно используют метиленхлорид.
Мировое производство
Поликарбонаты являются крупнотоннажными продуктами органического синтеза, мировые производственные мощности в 2006 года составляли более 3 млн тонн в год. Основные производители поликарбоната (2006)[1]:
Производитель | Объём производства | Торговые марки |
---|---|---|
Bayer Material Science AG | 900 000 т/год | Makrolon, Apec, Bayblend, Makroblend[2] |
Sabic Innovative Plastics | 900 000 т/год | Lexan |
Samyang Busines Chemicals | 360 000 т/год | Trirex[3] |
Dow Chemical / LG DOW Polycarbonate | 300 000 т/год | Calibre[4] |
Teijin | 300 000 т/год | Panlite[5] |
Всего | 3 200 000 т/год |
Применение
Благодаря сочетанию высоких механических и оптических качеств монолитный пластик также применяется в качестве материала при изготовлении линз, компакт-дисков, фар, компьютеров, очков и светотехнических изделий. Наиболее популярный в России формат применения — листовой поликарбонат: ячеистый («сотовый поликарбонат» или замковые панели сотового поликарбоната) и сплошной (монолитный поликарбонат). Листовой поликарбонат применяется в качестве светопрозрачного материала в строительстве. Также материал используется там, где требуется повышенная теплоустойчивость. Это могут быть светопрозрачные вставки в кровлю и фасадные конструкции, теплицы, навесы, шумовые ограждения дорог и так далее. Разнообразность применения листового поликарбоната связана с уникальным комплексом свойств: прозрачность, легкость, прочность, гибкость, долговечность (при наличии УФ защитного слоя). В мае 2015 года утвержден ГОСТ Р 56712-2015 «Панели многослойные из поликарбоната». Монолитный поликарбонат сертифицируется по ГОСТ Р 51136 «Защитные стекла».
Благодаря высокой прочности и ударной вязкости (250—500 кдж/м2) применяются в качестве конструкционных материалов в различных отраслях промышленности, используются при изготовлении защитных шлемов для экстремальных дисциплин вело- и мотоспорта. При этом для улучшения механических свойств применяются и наполненные стекловолокном композиции.
Стандартный поликарбонат не подходит для применений с длительным воздействием УФ-излучения. При этом происходит изменение оптических (помутнение, пожелтение) и механических (становится хрупким) свойств материала. Чтобы избежать этого, первичная смола может содержать УФ-стабилизаторы. Эти марки продаются как УФ-стабилизированный поликарбонат для литьевых и экструзионных компаний. Также поликарбонатные листы могут содержать анти-УФ-слой в качестве специального покрытия для повышения устойчивости к атмосферным воздействиям.
Поликарбонат был выбран в качестве материала для производства прозрачных вставок в медалях Зимних Олимпийских игр 2014 в Сочи, главным образом из-за его большого коэффициента теплового расширения, а также ввиду прочности, пластичности, удобства нанесения рисунка лазером[6].
Размеры и масса сотового поликарбоната
Размеры поликарбоната
Номинальная ширина стандартных панелей поликарбоната согласно ГОСТ Р 56712-2015 составляют 2100 мм. Номинальная длина: 6000 мм и 12000 мм. Однако в продаже чаще всего встречаются следующие типоразмеры (данные в формате: ширина х длина х толщина, мм):
- 2100 х 12000 х от 4 до 25;
- 2100 х 6000 х от 4 до 25.
Масса поликарбоната
Масса сотового поликарбоната чаще всего измеряется для квадратного метра определённой толщины[7]. Согласно ГОСТ Р 56712-2015 масса составляет:
- толщина: 4 мм, масса квадратного метра: 0,8 кг;
- толщина: 6 мм, масса квадратного метра: 1,3 кг;
- толщина: 8 мм, масса квадратного метра: 1,5 кг;
- толщина: 10 мм, масса квадратного метра: 1,7 кг.
См. также
Примечания
Поликарбонат Википедия
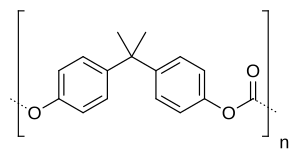
Поликарбонаты — группа термопластов, сложные полиэфиры угольной кислоты и двухатомных спиртов общей формулы (-O-R-O-CO-)n. Наибольшее промышленное значение имеют ароматические поликарбонаты, в первую очередь, поликарбонат на основе Бисфенола А, благодаря доступности бисфенола А, синтезируемого конденсацией фенола и ацетона.
История возникновения[ | ]
Первые упоминания о продукте, подобном поликарбонату, появились в XIX веке. В 1898 году получение поликарбоната впервые описал немецкий химик, изобретатель новокаина Альфред Эйнхорн. Тогда он работал у знаменитого химика-органика Адольфа фон Байера в Мюнхене и, занимаясь поиском обезболивающего средства из эфира, произвёл в лаборатории реакции хлорангидрида угольной кислоты с тремя изомерами диоксибензола и в осадке получил полимерный эфир угольной кислоты — прозрачное, нерастворимое и термостойкое вещество.
В 1953 году Герман Шнелл, специалист немецкой компании «BAYER», получил соединение поликарбоната. Этот полимеризированный карбонат оказался соединением, механические свойства которого не имели аналогов среди известных термопластов. В том же году поликарбонат запатентовали под маркой «Макролон».
Но в этом же 1953 году, всего несколькими днями позже, поликарбонат получил Дениель Фокс, специалист из известной американской компании «General Electric». Возникла спорная ситуация. В 1955 году её удалось решить, и компания «General Electric» запатентовала материал под маркой поликарбонат «Лексан». В 1958 году «BAYER», а затем в 1960 году «General Electric» пустили в промышленное производство технически пригодный поликарбонат. В дальнейшем права на «Лексан» были проданы компании «Sabic» (Саудовская Аравия).
Но это было всего лишь вещество-поликарбонат. До появления сотового (или ячеистого) поликарбоната как листового материала оставалось ещё долгих 20 лет.
В начале 1970-х годов в поисках альтернативы тяжёлому и хрупкому стеклу поликарбонатом заинтересовался Израиль, правительство которого активно поддерживало развитие сельского хозяйства и животноводчества в условиях жаркой пустыни. В частности, большое внимание уделялось теплицам, позволяющим выращивать растения в микроклимате, созданном с помощью капельного орошения. Стекло для изготовления теплиц было дорого и непрочно, акрил не мог удержать соответствующую температуру, а поликарбонат идеально для этого подходил.
Тогда совместно «General Electric» (владельцами сырья поликарбоната торговой марки «Лексан») проводились опыты по производству прозрачных пластиковых изделий на оборудовании компании «Polygal» в Рамат Ха-Шофете и Мегиддо (Израиль). Обе компании подгоняли технологию под сырьё, а сырьё — под технологию. Так, в Израиле в 1976 году получили первый в мире сотовый лист из поликарбоната[источник не указан 1160 дней].
Методы синтеза[ | ]
Синтез поликарбоната на основе бисфенола А проводится двумя методами: методом фосгенирования бисфенола А и методом переэтерификации в расплаве диарилкарбонатов бисфенолом А.
В случае переэтерификации в расплаве в качестве исходного сырья используется дифенилкарбонат, реакцию проводят в присутствии щелочных катализаторов (метилат натрия), температуру реакционной смеси повышают ступенчато от 150 до 300 °C, реакцию проводят в вакуумированных реакторах периодического действия при постоянной отгонке выделяющегося в ходе реакции фенола. Полученный расплав поликарбоната охлаждают и гранулируют. Недостатком метода является относительно небольшая молекулярная масса (до 50 КДа) получаемого полимера и его загрязнённость остатками катализатора и продуктов термодеструкции бисфенола А.
Фосгенирование бисфенола А проводят в растворе хлоралканов (обычно хлористого метилена CH2Cl2) при комнатной температуре, существует две мод
Сотовый поликарбонат Википедия
Структурная формула поликарбоната — эфира бисфенола АПоликарбонаты — группа термопластов, сложные полиэфиры угольной кислоты и двухатомных спиртов общей формулы (-O-R-O-CO-)n. Наибольшее промышленное значение имеют ароматические поликарбонаты, в первую очередь, поликарбонат на основе Бисфенола А, благодаря доступности бисфенола А, синтезируемого конденсацией фенола и ацетона.
История возникновения
Первые упоминания о продукте, подобном поликарбонату, появились в XIX веке. В 1898 году получение поликарбоната впервые описал немецкий химик, изобретатель новокаина Альфред Эйнхорн. Тогда он работал у знаменитого химика-органика Адольфа фон Байера в Мюнхене и, занимаясь поиском обезболивающего средства из эфира, произвёл в лаборатории реакции хлорангидрида угольной кислоты с тремя изомерами диоксибензола и в осадке получил полимерный эфир угольной кислоты — прозрачное, нерастворимое и термостойкое вещество.
В 1953 году Герман Шнелл, специалист немецкой компании «BAYER», получил соединение поликарбоната. Этот полимеризированный карбонат оказался соединением, механические свойства которого не имели аналогов среди известных термопластов. В том же году поликарбонат запатентовали под маркой «Макролон».
Но в этом же 1953 году, всего несколькими днями позже, поликарбонат получил Дениель Фокс, специалист из известной американской компании «General Electric». Возникла спорная ситуация. В 1955 году её удалось решить, и компания «General Electric» запатентовала материал под маркой поликарбонат «Лексан». В 1958 году «BAYER», а затем в 1960 году «General Electric» пустили в промышленное производство технически пригодный поликарбонат. В дальнейшем права на «Лексан» были проданы компании «Sabic» (Саудовская Аравия).
Но это было всего лишь вещество-поликарбонат. До появления сотового (или ячеистого) поликарбоната как листового материала оставалось ещё долгих 20 лет.
В начале 1970-х годов в поисках альтернативы тяжёлому и хрупкому стеклу поликарбонатом заинтересовался Израиль, правительство которого активно поддерживало развитие сельского хозяйства и животноводчества в условиях жаркой пустыни. В частности, большое внимание уделялось теплицам, позволяющим выращивать растения в микроклимате, созданном с помощью капельного орошения. Стекло для изготовления теплиц было дорого и непрочно, акрил не мог удержать соответствующую температуру, а поликарбонат идеально для этого подходил.
Тогда совместно «General Electric» (владельцами сырья поликарбоната торговой марки «Лексан») проводились опыты по производству прозрачных пластиковых изделий на оборудовании компании «Polygal» в Рамат Ха-Шофете и Мегиддо (Израиль). Обе компании подгоняли технологию под сырьё, а сырьё — под технологию. Так, в Израиле в 1976 году получили первый в мире сотовый лист из поликарбоната[источник не указан 1160 дней].
Методы синтеза
Синтез поликарбоната на основе бисфенола А проводится двумя методами: методом фосгенирования бисфенола А и методом переэтерификации в расплаве диарилкарбонатов бисфенолом А.
В случае переэтерификации в расплаве в качестве исходного сырья используется дифенилкарбонат, реакцию проводят в присутствии щелочных катализаторов (метилат натрия), температуру реакционной смеси повышают ступенчато от 150 до 300 °C, реакцию проводят в вакуумированных реакторах периодического действия при постоянной отгонке выделяющегося в ходе реакции фенола. Полученный расплав поликарбоната охлаждают и гранулируют. Недостатком метода является относительно небольшая молекулярная масса (до 50 КДа) получаемого полимера и его загрязнённость остатками катализатора и продуктов термодеструкции бисфенола А.
Фосгенирование бисфенола А проводят в растворе хлоралканов (обычно хлористого метилена CH2Cl2) при комнатной температуре, существует две модификации процесса — поликонденсация в растворе и межфазная поликонденсация:
При поликонденсации в растворе в качестве катализатора и основания, связывающего выделяющийся хлороводород используют пиридин, гидрохлорид пиридина, образующийся в ходе реакции, нерастворим в хлористом метилене и по завершении реакции его отделяют фильтрованием. От остаточных количеств пиридина, содержащегося в реакционной смеси, избавляются отмыванием водным раствором кислоты. Поликарбонат высаждают из раствора подходящим кислородсодержащим растворителем (ацетоном и т. п.), что позволяет частично избавиться от остаточных количеств бисфенола А, осадок сушат и гранулируют. Недостатком метода является использование достаточно дорогого пиридина в больших количествах (более 2 молей на моль фосгена).
В случае фосгенирования в условиях межфазного катализа поликонденсация проводится в два этапа: сначала фосгенированием бисфенолята А натрия получают раствор смеси олигомеров, которые содержат концевые хлорформиатные -OCOCl и гидроксильные -OH группы, после чего проводят поликонденсацию смеси олигомеров в полимер.
Переработка
При переработке поликарбонатов применяют большинство методов переработки и формовки термопластичных полимеров: литьё под давлением (производство изделий), выдувное литьё (разного рода сосуды), экструзию (производство профилей и плёнок), формовку волокон из расплава. При производстве поликарбонатных плёнок также применяется формовка из растворов — этот метод позволяет получать тонкие плёнки из поликарбонатов высокой молекулярной массы, формовка тонких плёнок из которых затруднена вследствие их высокой вязкости. В качестве растворителя обычно используют метиленхлорид.
Мировое производство
Поликарбонаты являются крупнотоннажными продуктами органического синтеза, мировые производственные мощности в 2006 года составляли более 3 млн тонн в год. Основные производители поликарбоната (2006)[1]:
Производитель | Объём производства | Торговые марки |
---|---|---|
Bayer Material Science AG | 900 000 т/год | Makrolon, Apec, Bayblend, Makroblend[2] |
Sabic Innovative Plastics | 900 000 т/год | Lexan |
Samyang Busines Chemicals | 360 000 т/год | Trirex[3] |
Dow Chemical / LG DOW Polycarbonate | 300 000 т/год | Calibre[4] |
Teijin | 300 000 т/год | Panlite[5] |
Всего | 3 200 000 т/год |
Применение
Благодаря сочетанию высоких механических и оптических качеств монолитный пластик также применяется в качестве материала при изготовлении линз, компакт-дисков, фар, компьютеров[уточнить], очков и светотехнических изделий. Наиболее популярный в России формат применения — листовой поликарбонат: ячеистый («сотовый поликарбонат» или замковые панели сотового поликарбоната) и сплошной (монолитный поликарбонат). Листовой поликарбонат применяется в качестве светопрозрачного материала в строительстве. Также материал используется там, где требуется повышенная теплоустойчивость. Это могут быть светопрозрачные вставки в кровлю и фасадные конструкции, теплицы, навесы, шумовые ограждения дорог и так далее. Разнообразность применения листового поликарбоната связана с уникальным комплексом свойств: прозрачность, легкость, прочность, гибкость, долговечность (при наличии УФ защитного слоя). В мае 2015 года утвержден ГОСТ Р 56712-2015 «Панели многослойные из поликарбоната». Монолитный поликарбонат сертифицируется по ГОСТ Р 51136 «Защитные стекла».
Благодаря высокой прочности и ударной вязкости (250—500 кдж/м2) применяются в качестве конструкционных материалов в различных отраслях промышленности, используются при изготовлении защитных шлемов для экстремальных дисциплин вело- и мотоспорта. При этом для улучшения механических свойств применяются и наполненные стекловолокном композиции.
Стандартный поликарбонат не подходит для применений с длительным воздействием УФ-излучения. При этом происходит изменение оптических (помутнение, пожелтение) и механических (становится хрупким) свойств материала. Чтобы избежать этого, первичная смола может содержать УФ-стабилизаторы. Эти марки продаются как УФ-стабилизированный поликарбонат для литьевых и экструзионных компаний. Также поликарбонатные листы могут содержать анти-УФ-слой в качестве специального покрытия для повышения устойчивости к атмосферным воздействиям.
Поликарбонат был выбран в качестве материала для производства прозрачных вставок в медалях Зимних Олимпийских игр 2014 в Сочи, главным образом из-за его большого коэффициента теплового расширения, а также ввиду прочности, пластичности, удобства нанесения рисунка лазером[6].
Теплица остеклённая листовым монолитным матовым поликарбонатом
Лист сотового поликарбоната толщиной 6 мм
Теплица из неокрашенного (бесцветного) сотового поликарбоната
Золотая олимпийская медаль Зимних Олимпийских игр 2014 года в Сочи
Размеры и масса сотового поликарбоната
Размеры поликарбоната
Номинальная ширина стандартных панелей поликарбоната согласно ГОСТ Р 56712-2015 составляют 2100 мм. Номинальная длина: 6000 мм и 12000 мм. Однако в продаже чаще всего встречаются следующие типоразмеры (данные в формате: ширина х длина х толщина, мм):
- сотового:
- 2100 х 12000 х от 4 до 25;
- 2100 х 6000 х от 4 до 25;
- монолитного:
- 2050 х 1250 х 1
- 2050 х 3050 х от 1,5 до 12
Масса поликарбоната
Масса сотового поликарбоната чаще всего измеряется для квадратного метра определённой толщины[7]. Согласно ГОСТ Р 56712-2015 масса составляет:
- толщина: 4 мм, масса квадратного метра: 0,8 кг;
- толщина: 6 мм, масса квадратного метра: 1,3 кг;
- толщина: 8 мм, масса квадратного метра: 1,5 кг;
- толщина: 10 мм, масса квадратного метра: 1,7 кг.
См. также
Примечания
Литература
- ГОСТ 25288-82 «Пластмассы конструкционные. Номенклатура показателей».
- ГОСТ Р 51136-2008 «Стёкла защитные многослойные. Общие технические условия».