Как скрепить две доски между собой, наращивание стропил
Соединение досок между собой по ширине и длине. Основные требования к рабочему процессу
Как соединить два бруса в длину:рекомендации мастеров и пошаговая инструкция
Устройство мансарды в значительной степени увеличивает жилую площадь дома. Практически, в доме появляется еще один эксплуатируемый этаж. Но для его полноценного использования необходимо выполнять укрепление чердачного перекрытия, так как нагрузки на конструкцию существенно возрастают. Прежде всего, это касается деревянных балок, чаще всего применяемых при возведении частных строений.
Специфика деревянных балок перекрытия
Популярность использования прогонов из дерева в чердачных перекрытиях связана с их легким весом по сравнению со стальными и железобетонными аналогами. К тому же, древесина обладает низкой теплопроводностью и малой звукопроницаемостью. Но натуральный материал, к сожалению, имеет ряд недостатков, которые необходимо учитывать. Это:
- отсутствие устойчивости к действию плесени, грызунов и насекомых;
- высокая пожароопасность;
- слабая прочность балок малого сечения.
С первыми двумя недостатками можно справиться путем обработки деревянных балок антисептиками и антипиренами. Последнюю же проблему решают путем использования пиломатериалов большего сечения или посредством укрепления несущих элементов перекрытия.
Балки чердачного перекрытия несут меньшие нагрузки по отношению к аналогичным межэтажным конструкциям.
При устройстве мансарды требуется усиление несущих деревянных элементов перекрытия. Если мероприятия не будут выполнены, то прогоны под увеличенной нагрузкой станут прогибаться и со временем безвозвратно деформируются. Это в лучшем случае, а в худшем – произойдет их растрескивание и, как результат, разлом. Но не стоит отчаиваться и думать, что столь желанное увеличение эксплуатируемой площади останется только в мечтах. Вариантов укрепления чердачных перекрытий существует достаточно много для того, чтобы выбрать единственно правильное решение, исходя из конкретных условий эксплуатации.
Когда требуется усиление
Следует отметить, что укреплять балочные конструкции требуется не только при сооружении мансарды, но и по другим веским причинам. А именно – при снижении несущих характеристик деревянных балок вследствие плохого состояния древесины, произошедшего в результате:
- неверных расчетов;
- повышенной влажности;
- случайного повреждения;
- жизнедеятельности насекомых-вредителей или грызунов;
- появления недопустимых прогибов;
- растрескивания;
- периодического воздействия непредусмотренных проектом временных нагрузок.
Профессионалы не рекомендуют надолго откладывать восстановительные работы. Несвоевременное решение проблемы может привести к печальным последствиям и даже трагедии. Для грамотной оценки предстоящих мероприятий разумнее будет пригласить специалиста.
Распространенные способы усиления деревянных балок
Диаметр бревен или сечение бруса для чердачного и межэтажного перекрытия выбирают с учетом нагрузок, приходящихся на квадратный метр площади пола или потолка в плане. При этом учитывается:
- ширина пролета;
- шаг деревянных балок.
В представленной ниже таблице можно увидеть оптимальные значения сечения бревен и пиломатериалов.
Укрепление чердачного перекрытия производится без изменения или с изменением условий работы балочной конструкции, с применением типовых или нестандартных решений. Выбор зависит от степени деформации древесины и конкретных требований по усилению прочностных характеристик прогонов и настила в целом. Наиболее распространенные варианты укрепления балок предусматривают использование:
- деревянных накладок;
- металлических пластин;
- прутковых протезов;
- углеволокна, называемого, также, углепластиком;
- подпоров в виде столбов.
Деревянные накладки и металлические пластины могут устанавливаться как в пролетной части деревянных балок, так и в местах их стыков с опорной стеной. Усиливающие элементы фиксируются с обоих боков или снизу и сверху ремонтируемого прогона. При этом накладки крепко стягиваются посредством болтов, пропущенных сквозь балки. Деревянные детали предварительно обрабатывают противогрибковыми составами и антипиренами. Металлические пластины окрашивают или наносят на их поверхность специальные средства, препятствующие ржавлению материала. Кроме того, древесину от металла отделяют слоем гидроизоляции.
Для обеспечения надежности балочной конструкции, накладки рекомендуется устанавливать по всей длине прогона.
Торцевые усиливающие элементы монтируют на участках, опирающихся на стены.
Подписка на новости сайта
В этом случае подгнившие концы балки обрезают, а удаленные куски заменяют:
- двойными деревянными накладками с установленными на уровне опорной части стены вкладышами, соответствующими толщине укрепляемой балки;
- концевыми металлическими протезами, выполненными из швеллера;
- металлическими полосами с хомутами;
- арматурными стержнями, скрепленными швеллерной обвязкой.
Список можно продолжить еще несколькими способами, в том числе передвижными протезами, сдвоенными системами и т.д., но они относятся к более сложным вариантам укрепления балок. Торцевое усиление имеет свою характерную особенность. Она заключается в устройстве временного подпора ремонтируемой балки столбом. После окончания работ он демонтируется.
Прутковые протезы представляют собой систему, состоящую из металлических хомутов, наложенных в нескольких местах поврежденной балки, и соединительных элементов. Последние изготавливаются из прочного стального профиля или нескольких арматурных прутьев, переплетенных между собой по «правилу треугольника». В этом случае система остается стабильной, без каких-либо пространственных подвижек. Вариант монтажа прутковых протезов зависит от степени требуемого усиления балочного перекрытия.
Армирование углеволокном относится к современным способам укрепления деревянных балок. Композитный материал пока еще не имеет широкого распространения, но технология, несомненно, относится к передовым методам. С нижней стороны прогона укладывается усиливающая конструкцию арматура. Далее углепластик в несколько слоев наклеивается на частично укрепленную балку, образуя корытообразный хомут. Легкость углеволокна, удобство в работе и отсутствие в конструкции малоэстетичных накладок являются несомненными преимуществами современного материала.
В случае неисправимых деформаций, поврежденный участок балки лучше будет удалить во избежание бесполезных затрат.
Простое решение
Наверное, самым востребованным должен быть наиболее простой вариант усиления чердачного перекрытия, а именно – установка столба, подпирающего проблемную балку. Этот незатейливый способ решает вопрос принятия нагрузок вертикальной опорой. Работы, в данном случае, сводятся лишь к монтажу столба. В результате, основная проблема исчезает, но на ее месте появляются две другие.
Один недостаток сводится к образованию точечной нагрузки, воздействующей на пол. Второй – связан с эстетической стороной вопроса. Дело в том, что столб, установленный посреди комнаты, будет смотреться нелепо. Но если его оригинально украсить, то опора может превратиться в интересный элемент декора, к тому же — функциональный.
Существует еще один способ укрепления чердачного перекрытия. Но его использование оказывается эффективным лишь в тех случаях, когда потолочные балки не имеют деформаций. Несущую способность конструкции увеличивают за счет установки дополнительных прогонов с обязательной обмоткой их торцов рубероидом. Защитные меры позволяют избежать механических повреждений и помогают противостоять воздействиям влаги.
Укрепление чердачного настила
Если усиление балок выполняется с целью дальнейшего устройства мансарды, то подумать об обновлении напольного настила все-таки придется. Опытные мастера рекомендуют воспользоваться плитами OSP. Их укладывают по черновому полу. В дальнейшем производят отделочные работы.
20.03.2017 в 20:03
Основные аспекты расчета деревянных балок и перекрытий
Перекрытие – очень важный конструктивный элемент любого здания, будь то частный дом или здание большого предприятия. Больше всего вопросов вызывает технология перекрытия. О том, как выполняется монтаж балок перекрытия, какие нюансы стоит при этом учитывать, мы и поговорим в данном материале.
Общая характеристика балок из дерева
При строительстве именно деревянные балки перекрытий считаются самым экономичным вариантом. Их монтаж не вызывает особых трудностей. Материал характеризуется низкой теплопроводностью, особенно по сравнению с железобетонными, стальными балками.
Конечно, есть у дерева и свои недостатки. Например, невысокая механическая прочность. Если металл поражает коррозия, то дерево – различные грибки и микроорганизмы. Вот почему перед установкой необходимо тщательно обрабатывать их различными антипиренами и антисептиками.
Основные требования к перекрытиям
Что такое перекрытие? Так называется горизонтальная конструкция, которая разделяет пространство сооружения по высоте. Именно благодаря ему можно ставить в помещениях сколько угодно мебели, размещать оборудование. Кроме того, соединение балок прочно связывает несущие стены, делает сооружение более устойчивым.
Каркас из досок своими руками. Сборка и крепление нижней обвязки
Деревянные балки перекрытий бывают цокольные, подвальные, чердачные и междуэтажные.
Балка перекрытия из дерева должна соответствовать следующим требованиям:
- Прочность. Поскольку речь идет о достаточно серьезных нагрузках, материал должен выдержать их. Учитывайте постоянное давление и переменное.
- Жесткость. Насколько используемый материал способен сопротивляться изгибу?
- Тепловая и звукоизоляция.
- Пожарная безопасность.
Разновидности перекрытий: какие бывают?
В зависимости от назначения, можно выделить такие разновидности перекрытий:
- Цокольное. Поскольку оно является основой для пола, к балкам предъявляются повышенные требования. Стоит ли говорить, насколько прочными они должны быть?
Небольшой совет. Если планируете строить гараж или подвал под 1-м этажом, перекрытие лучше делать по балкам, сделанным из металла. Дерево подвержено гниению, выдержать солидную нагрузку сможет далеко не всегда.
- Чердачное.
- Междуэтажное.
Деревянные балки перекрытий бывают:
- Цельные. Производятся из твердых пород – как хвойных, так и лиственных.
- Клееные. Благодаря данной технологии, возможно изготовление планок приличной длины – вплоть до двадцати метров. Обладают повышенной прочностью, способны выдержать очень большие нагрузки. Еще одна особенность – идеально гладкая поверхность. Благодаря ей, снизу дерево оставляют открытым – оно становится настоящей изюминкой помещения.
Тонкости расчетов
Итак, вы поставили цель определить, сколько балок понадобится для перекрытия. Чтобы сделать это, необходимо:
- Выполнить замеры пролета, который планируете перекрывать.
- Выяснить, какой способ крепежа на стене будет наиболее оптимальным.
- Рассчитать нагрузку.
- Подобрать нужный шаг и сечение, используя таблицы или специальный калькулятор.
Балки перекрытия: определение длины
Расчет длины выполняется в соответствии с размерами пролета, который будут перекрываться, а также глубиной заделывания в стены. Чтобы измерить длину пролета, воспользуйтесь рулеткой. Что касается глубины заделывания, во многом она зависит от материала.
Когда дом построен из кирпичей или блоков, балки перекрытия заделывают в «гнезда» глубиной 10 см и более (доска), 15 см и более (брус). Если сооружение деревянное, материал монтируется в отдельные зарубки глубиной минимум 7 см. Используете металлические крепления? В таком случае, длина балок и пролета будет одинаковой. Также допускается вариант, когда в процессе монтажа стропильных ног они выпускаются наружу, примерно на 30-40 сантиметров за пределы стен. Так формируется свес.
Оптимальным будет вариант, когда балки перекрытий деревянные используются для перекрытия пролетов в 250 – 400 сантиметров. Когда пролет достаточно длинный (более 4 метров), на помощь приходят современные конструкции из клееного бруса.
Как определить нагрузку?
Для начала давайте выясним, что представляет собой такая нагрузка. Она состоит из:
- Нагрузки элементов перекрытия.
- Эксплуатационного давления бытовых устройств, людей и пр. Расчет нагрузки достаточно громоздкий, обычно выполняется опытными специалистами. Однако вы всегда сможете сделать его самостоятельно. Предлагаем упрощенный вариант, с которым мы познакомим вас ниже.
А начнем мы с расчета перекрытия для чердака, на котором не планируется укладка крупногабаритных вещей, утеплитель будет легким (например, минеральная вата). Согласно предписанию СНиП 2.01.07-85, нагрузка составит:
- 70 х 1,3 = 90 кг/м2. В данной схеме 70 – норма нагрузки в килограммах на один квадратный метр, а 1,3 – запас. Общая расчетная нагрузка рассчитывается следующим образом: Робщ.=Рсобств.+Рэкспл. = 50+90=130 кг\м2. Округлим полученное значение в лучшую сторону и получим 150 кг/м2.
- Планируя другой, более громоздкий утеплитель, и хранение различных вещей на чердаке, нормативное значение нагрузки желательно увеличить до 150 килограмм на м2. Что касается общей нагрузки, она составит: 50+150х1,3 = 245 кг/м2.
- Есть еще и третий вариант, когда чердак используют для обустройства мансарды. Расчетная нагрузка при этом возрастает до 300 кг/м2.
Запомните одно простое правило: жесткость и прочность всего перекрытия зависит скорее от высоты балок, нежели от ширины. Поскольку на конструкцию действуют два вида нагрузки (сосредоточенная и распределенная), проектировать перекрытия нужно с небольшим запасом прочности. Это гарантирует, что эксплуатация перекрытия будет не только долговечной, но и безопасной.
Деревянные балки перекрытий: как узнать шаг, сечение?
Когда знаешь нужную длину каждой балки перекрытия из дерева, расчетную нагрузку, несложно узнать сечение, шаг укладки. По мнению большинства инженеров и специалистов в области строительства, универсальным вариантом будет прямоугольное сечение с соотношением ширины/высоты 1:1,4 (S и H соответственно).
Ширина балок может варьироваться от 4 до 20 сантиметров, высота – от 10 до 30 см. Когда с этой целью используются бревна, их диаметр варьируется от 11 сантиметров до 30.
Теперь давайте поговорим о шаге балок. В зависимости от вида, он варьируется в пределах 30-120 сантиметров. Если здание каркасное, необходимо, чтобы шаг укладки был таким же, как шаг стоек. Это позволит добиться максимальной жесткости.
Подведем итог вышесказанного. Вы только что узнали, как рассчитывать шаг и длину деревянных балок перекрытия, выполнять некоторые другие расчеты. Данный материал будет полезен всем, кто занимается строительством или хотел бы лично проконтролировать правильность расчетов, выполненных другими специалистами.
10 простых советов для идеальных соединений на «Ус»
Что может быть проще соединения деревянных деталей на «ус»? Не смотря на простоту метода, порой возникают сложности с точностью и аккуратностью соединений. В этой статье мы дадим вам простые советы, взяв на вооружение которые, вы достигнете невероятных результатов. Ваши угловые соединения будут всегда идеальными!
1. Подбирайте направление и структуру волокон
Не важно что вы делаете: рамку для фотографий или обвязку для мебельного фасада, убедитесь что цвет древесины, а так же направление и структура волокон на заготовках совпадают. Подбор деталей со схожей структурой занимает немного времени, но в результате вы получаете превосходные соединения.
2. Тонкая настройка угла реза с помощью липких листков бумаги
Если вы когда-нибудь пробовали отрегулировать ваш торцовочный станок на несколько десятых градуса, то вы знаете как трудно это сделать. Предлагаем вам простой способ решения этой задачи: наклейте на поперечный упор несколько листков бумаги для заметок. Таким образом, делая пробные резы и убирая по одному листку вы достигнете идеального угла реза3. Используйте обрезки заготовок для примерки деталей
Чтобы точно определить длину элемента обвязки, необходимо примерить ее к панели. Это легко сделать если закрепить на панели обрезки обвязки
4. Применяйте шпонки для ровных соединений
Зачастую не просто ровно расположить детали относительно друг друга и зажать в струбцинах, особенно когда детали смазаны скользким клеем. Именно поэтому деревообработчики используют шпонки, даже в тех случаях когда дополнительная прочность соединения не требуется.
5. Собирайте рамочные конструкции на угловые струбцины
На некоторых струбцинах при сборке рамок вам надо дополнительно убедиться что все углы соединены под 90 градусов. Используя угловые струбцины необходимость в дополнительных замерах углов и выставления диагоналей отпадает.
6. Увеличьте «открытое время» вашего клея
Порой трудно быстро нанести клей на соединения, собрать рамки и зажать их в струбцинах без спешки и суеты до того, как клей начнет схватываться (зачастую открытое время клея составляет менее 5 минут в теплом и сухом помещении). Что бы увеличить открытое время клея, вы можете слегка разбавить его водой. Однако, не переусердствуйте — если воды будет слишком много, то прочность соединения может уменьшиться
7. Сначала соберите детали на «ус», потом профилируйте
Профилированные заготовки не всегда удобно торцевать — могут появиться сколы, их не всегда легко зажать в струбцинах — можно повредить наружный профиль изделия. Поэтому упростите свою жизнь — сначала соберите и склейте рамку из заготовок прямоугольного сечения, а после того как клей высохнет отпрофилируйте ручным фрезером или на фрезерном станке8. Доверьтесь своему осязанию
Когда вы делаете рамочную конструкцию, детали на противоположных сторонах изделия должны быть одинаковой длины. Что бы в этом убедиться проведите простой тест. Сложите две детали вместе и проведите пальцем по торцам. Не должно быть никаких перепадов. Вы можете не заметить разницу по длине на глаз, но вы обязательно почувствуете даже минимальное несовпадение длины заготовок.
9. Закрывайте некрасивые щели
Если в процессе сборки изделий вам все же не удалось избежать щелей на углах соединений, не стоит отчаиваться. Просто закройте их, придавив углы к центру соединения тупым гладким предметом. Вы удивитесь, но щель исчезнет, при этом внешний вид изделия нисколько не испортится. Поверьте, даже опытные мастера пользуются этим способом.
10. Вы можете изменить пропорции изделия в случае ошибки
Если последняя деталь вашей обвязки получилась чуть короче противоположной, можно обрезать ее по внутренней части. А после сборки обрезать остальные детали по внешней стороне. Таким образом ширина обвязки несколько уменьшится. Если это, например, не мебельный фасад, то никто и ничего не заметит
Технология склеивания массивной древесины
Содержание страницы
1. Способы склеивания массивной древесины по длине
1.1. Виды шиповых соединений
Очень часто при изготовлении различных изделий из древесины необходимо соединить разные детали склеиванием. Применение шипового соединения придает изделию необходимую прочность.
Шиповое соединение состоит из двух частей — шипа и гнезда проушины. Шип — это выступ, который находится на конце одной из соединяемых деталей. Шип вставляется в проушину либо гнездо другой соединяемой детали. Можно встретить одинарный (рис. 1), двойной (рис. 1) и многократный шипы (рис. 1). Шипы делятся на цельные и вставные. Цельным называется шип, который составляет с деталью единое целое. Вставной шип выполняется отдельно от детали. Помимо приведенных существует еще несколько цельных шиповых соединений: «ласточкин хвост» (рис. 1, ), зубчатое соединение (рис. 1).
Кроме повышения прочности изделия шиповое соединение может применяться с целью повышения полезного выхода. На рисунке показан мебельный щит с сучками и без сучков.
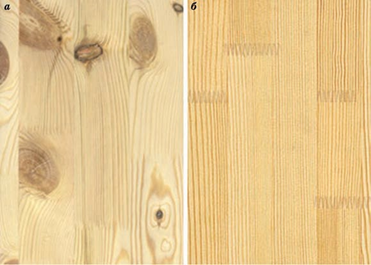
Мебельный щит без сучков имеет лучший внешний вид по сравнению с предыдущим.


Рис. 1 Виды шипов: а — одинарный; б — двойной; в — круглый; г — односторонний «ласточкин хвост»; д — многократный; , е,ж — «ласточкин хвост»; з — зубчатый.
Как известно, существуют различные виды пороков строения древесины, которые могут значительно ухудшить внешний вид изделия. К ним относят сучки, трещины, обзол и др. (рис. 2). Эти пороки выпиливают (рис. 3), фрезеруют шиповое соединение (рис. 4), оставшиеся части брусков сращивают по длине. Зубчатый шип некоторым образом зрительно ухудшает внешний вид, поэтому такие детали применяются под покраску (рис. 5).
Склеивание короткомерных пиломатериалов из массивной древесины по длине позволяет повысить полезный выход. Склеивание в торец характеризуется низкой прочностью (менее 10% прочности натуральной древесины) и поэтому не применяется. Склеивание на ус (рис. 6) является достаточно прочным соединением. Однако при этом требует большой длины шипа и как следствие увеличения расхода материала. Склеивание на зубчатый шип (рис. 6) наиболее предпочтительно, так как обеспечивает 50–60% прочности от цельной древесины.
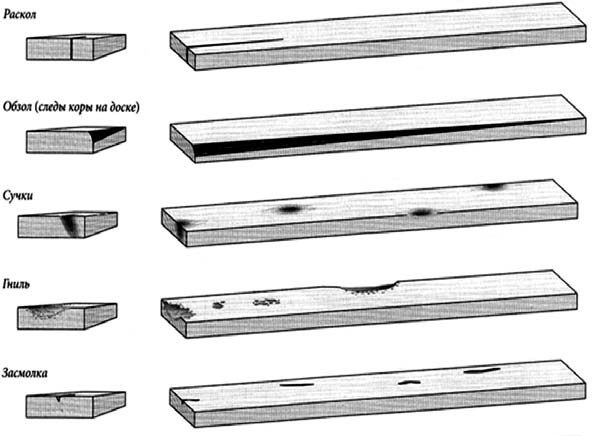
Рис. 2 Пороки строения древесины в пиломатериалах
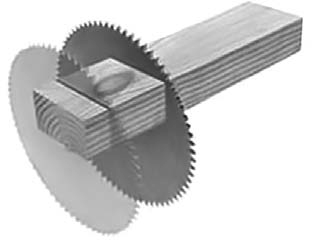
Рис. 3 Схема удаления пороков
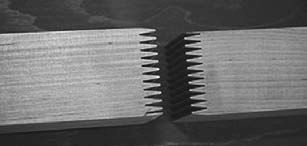
Рис. 4 Зубчатое шиповое соединение
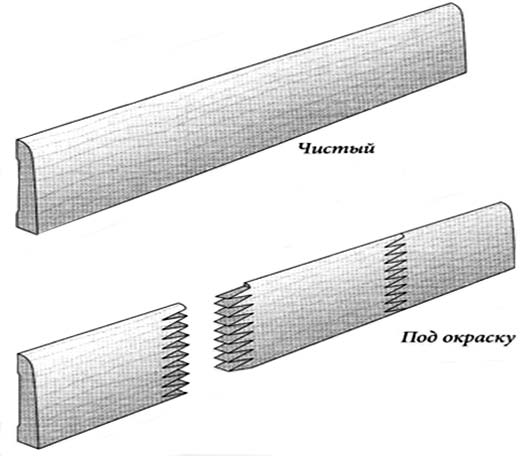
Рис. 5 Склеивание по длине
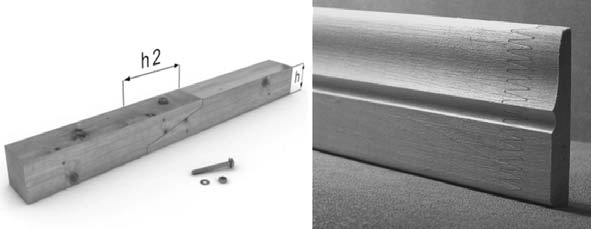
Рис. 6 Виды зубчатого шипового соединения: а — склеивание на ус; б — склеивание на зубчатый шип.
1.2. Параметры зубчатого шипового соединения
Горизонтальные шипы применяются в соединениях, не требующих высоких прочностных свойств, вертикальные шипы — в конструкционных соединениях.
Зубчатое соединение характеризуется шагом, длиной и величиной затупления (рис. 7).
Зазор необходим для удаления излишков клея. Длина шипа выбирается в зависимости от назначения (обшивка, наличник — 5 мм; настил — 30 мм).
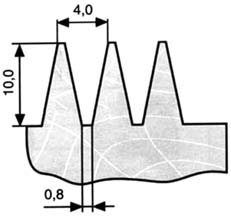
Рис. 7 Параметры зубчатого шипа
Вид применяемого при склеивании клея выбирается в зависимости от назначения. Поливинилацетатные, карбамидоформальдегидные и казеиновые клеи применяются при изготовлении изделий, эксплуатируемых внутри помещений; фенолоформальдегидные — для изделий, эксплуатируемых снаружи помещений.
Формирование шипа производится в два этапа: выравнивание поверхности (чистовая торцовка) и фрезерование шипа на фрезерных или шипорезных станках. С противоположной стороны бруска шаг зубчатого соединения должен быть смещен на полшага.
1.3. Технология склеивания по длине
Склеивание заготовок по длине выполняется в следующей последовательности. Вначале производится продольный раскрой на многопильных станках. Затем поперечный раскрой на кратные заготовки с удалением дефектных мест (рис. 8).
Для фрезерования зубчатого шипа применяются фрезы (рис. 9).
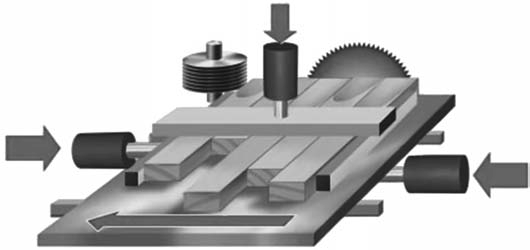
Рис. 8 Выпиливание дефектных мест
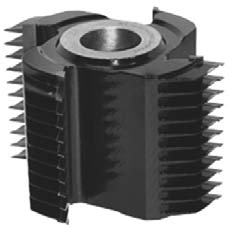
Рис. 9 Фреза для фрезерования зубчатого шипа
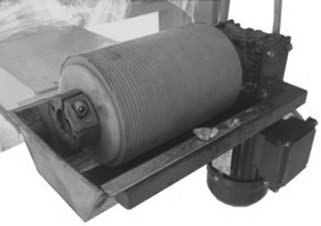
Рис. 10 Клеевые вальцы
Нанесение клея может быть осуществлено кистью, окунанием или гребенчатыми клеевыми вальцами (рис. 10). Расход клея составляет до 400 г/м2.
Лучшим способом является склеивание брусков бесконечной длины с последующим их раскроем на требуемый размер (см. рис. 11).
Сборка и запрессовка производится в пневматических или гидравлических ваймах (см. рис. 12). Горизонтальное давление обеспечивает плотный контакт зубчатого соединения. А вертикальное давление создается для предотвращения выгибания заготовки.
Продолжительность запрессовки с выдавливанием излишков клея составляет 2 с. Отверждение клея происходит вне установки. Сила и надежность самозаклинивания достаточны для раскроя сразу после склеивания. Прочность склеивания характеризуется пределом прочности при статическом изгибе.
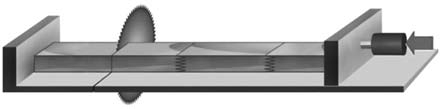
Рис. 11 Схема сращивания брусков с последующим их раскроем на требуемый размер
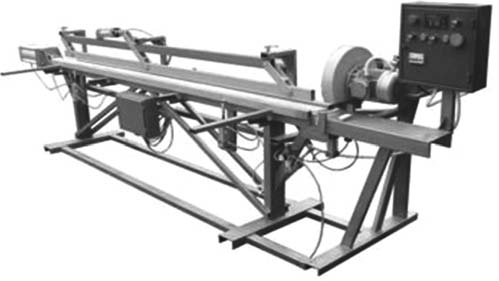
Рис. 12 Вайма для склеивания на зубчатый шип
2. Технология изготовления мебельных щитов
2.1. Схема технологического процесса изготовления мебельных щитов из массивной древесины
Мебельный щит склеивается из деревянных строганых брусков (реек) шириной от 10 до 50 мм. При изготовлении мебельных щитов применяется древесина хвойных и лиственных пород. Мебельные щиты применяются при изготовлении столярно-строительных изделий, деталей интерьера, но чаще всего в мебельном производстве.
Схема технологического процесса изготовления мебельных щитов из массивной древесины представлена на рисунке 13.
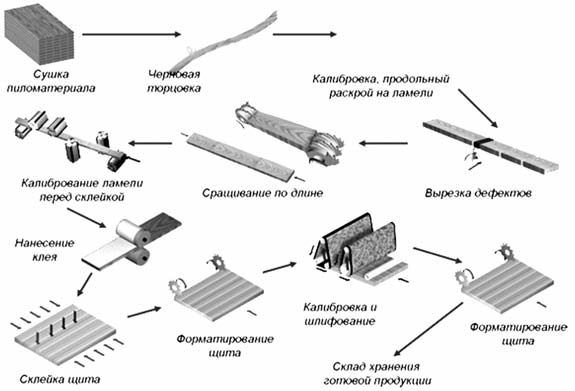
Рис. 13 Схема технологического процесса изготовления мебельного щита
Для склеивания мебельных щитов используют бруски (ламели), из которых удалены дефекты и сращенные по длине. Нанесение клея на поверхность производят ручным способом (рис. 14) или при помощи клеевых вальцов.
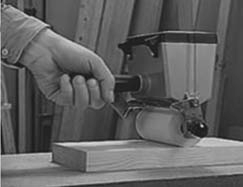
Рис. 14 Нанесение клея ручным способом
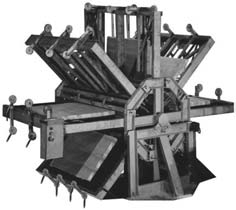
Рис. 15 Веерная вайма с механическим зажимом
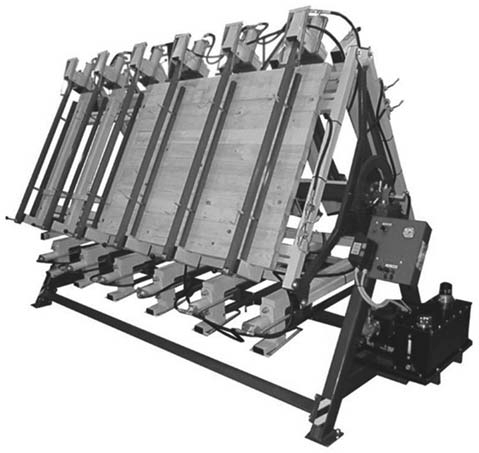
Рис. 16 Ваймы с гидравлическим зажимом
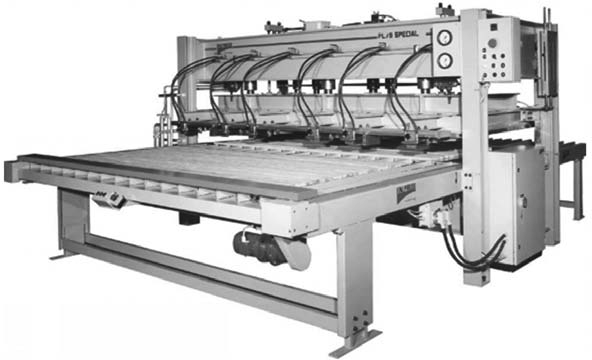
Рис. 17 Одноэтажный гидравлический пресс для склеивания мебельных щитов
Для склеивания могут применяться ваймы, в которых зажим брусков с нанесенным клеем механический. Для увеличения производительности их делают веерными (см. рис. 15). При склеивании щитов также могут применяться ваймы (прессы) с гидравлическим зажимом (рис. 16). Склеенные в ваймах бруски могут быть смещены относительно друг друга, что потребует выравнивания поверхности щитов в рейсмусовых станках.
Этого недостатка лишены щиты, склеенные в одно( этажных гидравлических прессах (рис. 17).
Поверхность щитов получается более ровной, и в этом случае не требуется обработка в рейсмусных станках. Для уменьшения продолжительности склеивания плиты пресса выполнены обогреваемыми. При изготовлении мебельных щитов необходимо соблюдать следующие правила.
- Склеиваемые бруски для предотвращения коробления должны собираться «вразбежку» (в соседних брусках направление волокон не должно совпадать).
- Ширина брусков должна быть кратной двум-трем толщинам = (2–3).
- Промежуток времени от нанесения клея на поверхность до склеивания не должен превышать 5 мин.
- Боковые поверхности реек для предотвращения появления щелей между ними должны быть строго перпендикулярны пласти.
- Склеиваемые бруски не должны быть покоробленными и их желательно склеивать сразу после строгания.
- Влажность древесины должна быть 8 ± 2%.
- Расход клея 180–220 г/м2. После склеивания щи( тов должна быть предусмотрена технологическая выдержка в плотных стопах в течение 5–24 ч.
- В верхних щитах пачки могут подсыхать верхние слои после склеивания. Для предотвращения коробления верхних щитов всю пачку необходимо укрывать полиэтиленом.
- Щиты длиной более 2 м подвергаются короблению в большей степени, чем короткие, к тому же их труднее обрабатывать. Поэтому лучше склеивать заготовки не( больших размеров.
2.2. Форматная обрезка и шлифование мебельных щитов
После склеивания производится обрезка мебельных щитов по формату (рис. 18) на форматно-обрезных станках. Для предотвращения образования сколов на поверхности щита в обрезных станках должны быть установлены подрезатели (рис. 19).
Готовые плиты имеют значительную разнотолщинность. Кроме того, на поверхности плит могут быть раз, личные дефекты — вмятины, загрязнения и т. д. По, этому после склеивания и выдержки щитов производят шлифование их поверхности на широколенточных шлифовальных станках. Обработка производится шлифовальными лентами разной зернистости в два этапа (рис. 20).
Вначале шлифовальными лентами более крупной зернистости снимают примерно 70% от величины припуска (калибруют), затем лентами с более мелкой зернистостью снимают оставшийся припуск (рис. 21). На первом этапе шлифования применяют отечественные шлифовальные ленты с номером зернистости 40–50, импортные — 36–40. На втором этапе шлифования применяют ленты с номером зернистости отечественные 16–25, им, портные — 80–100. Общий припуск на шлифование составляет 1–2 мм.
Сортируют плиты в зависимости от количества и видов дефектов строения древесины на поверхности (рис. 22) и от дефектов обработки поверхности. Качество склеивания оценивают по прочности при скалывании по клеевому слою (не менее 4 МПа).
Также контролируют предел отклонения размеров разных длин диагоналей, шероховатость, покоробленность. Качественные показатели мебельных щитов регламентируются требованиями заказчика или нормативных документов. Хранят плиты в сухих отапливаемых помещениях.
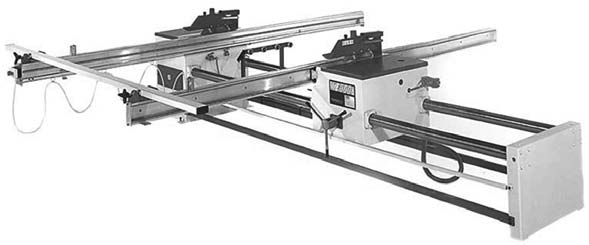
Рис. 18 Форматно-обрезной станок для обрезки кромок по формату
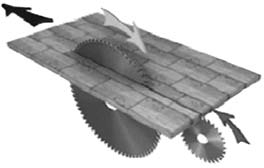
Рис. 19 Применение подрезателей при обрезке щитов
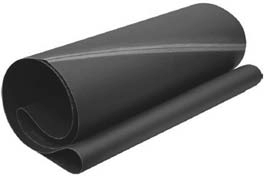
Рис. 20 Широкие шлифовальные ленты для обработки поверхности мебельных щитов
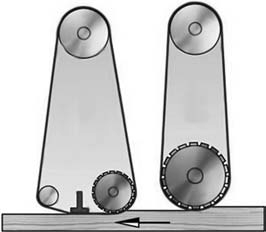
Рис. 21 Схема двухэтапной обработки мебельных щитов в шлифовальных станках
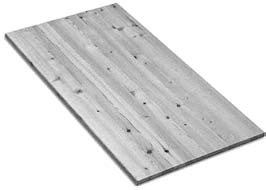
Рис. 22 Мебельный щит
3. Клееные деревянные конструкции
3.1. Преимущества клееных деревянных конструкций
Клееные деревянные конструкции применяют при изготовлении конструкций и изделий строительного назначения.
Благодаря легкости, прекрасным эстетическим и теплотехническим свойствам, высокой прочности и огнестойкости клееная древесина все чаще используется в объектах строительства и реконструкции. С ее применением можно создавать покрытия зданий различного назначения пролетами до 100 м. Богатый опыт применения этого материала позволяет использовать его в строительстве как жилых, так и производственных или общественных зданий любой сложности.
Несмотря на то что клееные деревянные конструкции являются достаточно новым материалом, они могут беспрепятственно применяться не только в малоэтажном домостроении, но и в таких социально значимых объектах, как спорткомплексы, аквапарки, торговые центры, мосты. Естественно, проекты должны соответствовать всем существующим строительным нормативам и требованиям. Если есть какие%то отступления, то в проекте могут быть предусмотрены компенсирующие мероприятия (покрытие конструкций защитными пропитками) или разработка специальных технических условий.
Для изготовления клееных деревянных конструкций применяют древесину хвойных и лиственных пород. Породу древесины определяют по назначению и условиям эксплуатации конструкций. Для изготовления несущих конструкций используются в основном пиломатериалы хвойных пород (сосна, ель, лиственница) не ниже II сорта по ГОСТ 1713%2007. Для изготовления ненесущих конструкций используются в основном пиломатериалы хвойных пород (сосна, ель, лиственница) не ниже III сорта по ГОСТ 1713-2007.
Безопасность и долговечность деревянных клееных конструкций в определенной степени зависит от типа и марки применяемого клея, его эксплуатационных и технологических свойств. К основным эксплуатационным свойствам клеев, применяемых в производстве клееной древесины, относят прочность клеевого соединения, т. е. его способность сохранять прочность в течение заданного срока эксплуатации изделий; эластичность клеевого соединения; водостойкость как способность клеевого соединения сохранять прочность после длительного или интенсивного воздействия воды на изделия; морозостойкость, биостойкость, температуро- и пожаростойкость, т. е. способность клея сохранять прочность при воздействии высоких температур и открытого огня. Клеевые системы характеризуются разнообразием композиций смол с различными свойствами, используемых отвердителей и наполнителей, способами нанесения клея.
При выборе средств и способов защиты деревянных клееных конструкций основное внимание должно быть обращено на предохранение их от переменного увлажнения и высушивания. При соблюдении требований конструкционной профилактики вероятность выхода из строя деревянных клееных конструкций массивного сечения в зданиях в результате биоразрушения столь незначительна, что подвергать их биозащитной обработке, как правило, не требуется.
По функциональному назначению средств для обработки клееных деревянных конструкций можно разделить на четыре основные группы:
- декоративные;
- влагозащитные;
- биозащитные;
- огнезащитные.
На практике часто приходится сталкиваться с необходимостью проведения комплексной и комбинированной обработки клееной древесины. Например, если в процессе эксплуатации не исключено увлажнение древесины, способное привести к появлению грибов, то необходимо предусмотреть защиту клееных деревянных конструкций не только от биоразрушения, но и от увлажнения.
В ряде случаев помимо биовлагозащитной обработки по требованиям пожарной безопасности необходима огнезащита клееных деревянных конструкций. Для защиты торцов массивных клееных элементов от увлажнения и расслаивания при эксплуатации в условиях повышенной или переменной влажности используют гидроизолирующие мастичные составы.
Применению клееной древесины в качестве конструкционного материала способствует целый ряд ее свойств:
- малая собственная масса при высокой прочности;
- высокая заводская готовность конструкций;
- технологичность изготовления изделий различных габаритов и форм; простота сборки и обработки конструкций на строительной площадке;
- восполняемость сырьевой базы.
В гражданском строительстве клееные деревянные конструкции привлекают возможностью создания разнообразных конструктивных схем, в том числе пространственных.
Важным отличием деревянных клееных конструкций от железобетонных и металлических является простота изготовления индивидуальных изделий. В гражданских зданиях типа спортзалов, крытых рынков, манежей, павильонов использование клееных деревянных конструкций снижает вес покрытия в 4–5 раз, трудоемкость монтажа до 20%, расход стали до 50%.
Достоинство деревянных клееных конструкций — возможность создания конструкций практически любых размеров и форм. Однако проектирование и изготовление оригинальных конструкций целесообразно лишь для отдельных зданий и сооружений, в том числе уникальных по размерам или по техническому решению. В остальных случаях следует использовать унифицированные конструкции и их элементы, более доступные для серийного изготовления.
3.2. Технологический процесс изготовления клееных деревянных конструкций
Схема технологического процесса изготовления клееных деревянных конструкций приведена в таблице 1.
Технологический процесс изготовления клееного бруса для несущих конструкций рассмотрим на примере предприятия «Нижегородский деревообрабатывающий комбинат» ДОК-78.
Таблица 1. Схема технологического процесса изготовления клееных деревянных конструкций
Технологический процесс производства клееного бруса начинается на складе, где осуществляется сортировка лесоматериалов хвойных пород, после чего производится изготовление на лесопильном станке обрезных пиломатериалов (рис. 23).
Далее производится сушка пиломатериалов в сушильных камерах с автоматическим программированием управления, функциями нагрева, вентиляции и увлажнения (рис. 24).
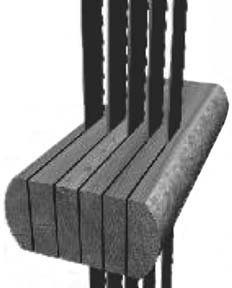
Рис. 23 Изготовление обрезных пиломатериалов
Четырехсторонний станок продольного фрезерования обрабатывает стороны ламелей для придания правильных геометрических размеров и вскрытия дефектов (см. рис. 25). Из станка выходят гладкие заготовки требуемых размеров прямоугольного сечения с прямой кромкой.
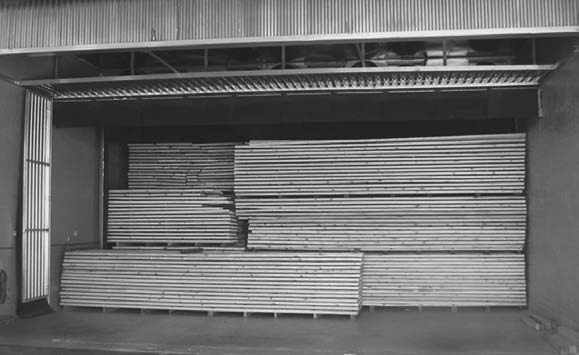
Рис. 24 Сушилка с пакетами пиломатериалов
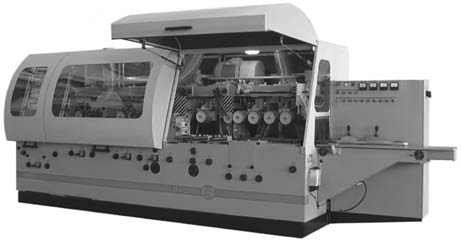
Рис. 25 Четырехсторонний строгальный станок
Автоматический торцовочный станок линии оптимизации осуществляет вырезку промаркированных оператором пороков в автоматическом режиме. Пороки маркируются флуоресцентным мелом, который распознается расположенной на пиле камерой. При наличии трещин на торцах досок они автоматически выпиливаются без предварительной маркировки. Отходы отбрасываются, а кондиционные заготовки направляются к линии сращивания в длину на зубчатый шип.
На линии сращивания сначала фрезеруют на торцах заготовки зубчатый шип, а затем наносят на них клей и прессуют заготовки в доску или балку бесконечной длины, которая затем торцуется на требуемые размеры. После чего производится технологическая выдержка для отверждения клея продолжительностью до 8 ч в зависимости от вида клея.
Четырехсторонний станок продольного фрезерования осуществляет строгание ламелей с верхней и нижней пластей детали.
Клеенаносящий станок (рис. 26) осуществляет нанесение клея на поверхность детали, после чего заготовки подаются в пресс для склеивания (рис. 27).
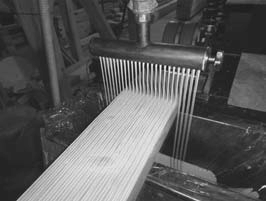
Рис. 26 Нанесение клея на поверхность детали
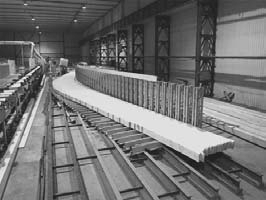
Рис. 27 Пресс для склеивания клееных деревянных конструкций
Режим прессования:
- температура помещения, °C 16;
- температура клея, °C 18 ± 1;
- жизнеспособность клея, ч 2–4;
- расход клея, г/м2 250–350;
- время открытой выдержки (от нанесения клея до сборки), мин 10;
- время закрытой выдержки (от сборки до запрессовки), мин 30;
- давление, МПа 3–5;
- время прессования, ч 8–10;
- время выдержки после запрессовки, ч 8. Транспортировка склеенных заготовок осуществляется цеховым краном.
Станок продольного фрезерования балок выполняет двух- или четырехстороннюю обработку прямых или гнутых балок с фаской или без. В настоящее время для этих целей используются станки с рабочей шириной от 400 до 2600 мм. При производстве только прямых балок перед и после станка должен располагаться роликовый транспортер, для прямых и гнутых балок необходима подвижная тележка, так как сам строгальный станок установлен на поворотном круге и поворачивается в зависимости от радиуса балки. Укладка детали перед станком и съем ее после обработки осуществляется с помощью крана, а для небольших изделий — с помощью штабелеукладчика.
К оборудованию для завершающих операций относятся станок для торцовки и раскроя балок и бруса и обрабатывающий центр. Также требуется многочисленный ручной инструмент, применяющийся для формирования различных врезок, сверления и фрезерования, необходимого для строительных конструкций.
С помощью толкателя брус роликовым транспортером направляется в торцовочный станок, где сначала производится врезание, а затем балка раскраивается на длины в соответствии с заданной программой.
Операция упаковки необходима для защиты балок при транспортировке от загрязнения и влажности. Обычно изделия оборачивают пленкой (стандартными считаются сечения от 6×12 до 16×36 см и длиной 12–18 м) и затем укладывают на склад временного хранения.
Для защиты от увлажнения и разрушения клеевого слоя на торцовые поверхности конструкции наносят эпоксидную шпатлевку на рабочем месте.
Режим нанесения шпатлевки:
- температура воздуха, °C 18–20;
- относительная влажность, % 65–75;
- расход шпатлевки, кг/м2 1,9.
Следующей операцией по изготовлению клееных конструкций является отделка, которая осуществляется на отделочных участках. Конструкции укладываются в пакеты и с помощью крана подаются на транспортные тележки и удаляются из цеха для дальнейшей обработки. Обрезки, стружка, опилки удаляются с помощью пневматического транспорта.
4. Технология клееного бруса
4.1. Область применения клееного бруса
Изготовление деталей строительного назначения из клееного бруса значительно улучшает прочностные и эксплуатационные характеристики изделий. Балки из клееного бруса используются при устройстве полов, крыш и потолков (рис. 28). Также из клееного бруса изготавливаются стены (рис. 29).
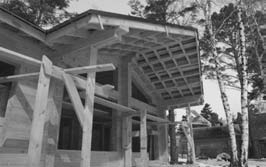
Рис. 28 Применение клееного деревянного бруса в деревянном домостроении
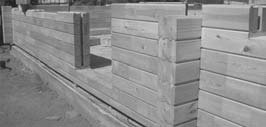
Рис. 29 Стены дома из клееного бруса
Клееный брус применяется при изготовлении деревянных окон (рис. 30).

Рис. 30 Применение клееного бруса при изготовлении окон
4.2. Основные операции технологического процесса изготовления клееных деревянных конструкций
Схема технологического процесса изготовления клееных деревянных конструкций приведена на рисунке 31. Технологический процесс изготовления клееного бруса состоит из следующих основных операций (рис. 32–41):
- поперечный раскрой пиломатериалов и вырезка дефектных мест на торцовочном станке;
- фрезерование зубчатого шипа;
- склеивание заготовок по длине;
- предварительная торцовка пиломатериала на торцовочном станке;
- строгание ламелей с четырех сторон на четырехстороннем строгальном станке;
- нанесение клея на поверхность ламелей;
- склеивание заготовок на гидравлическом вертикальном прессе;
- фрезерование профиля заготовки;
- чистовая торцовка в размер;
- выпиливание или фрезерование пазов под сборочные элементы;
- упаковка.
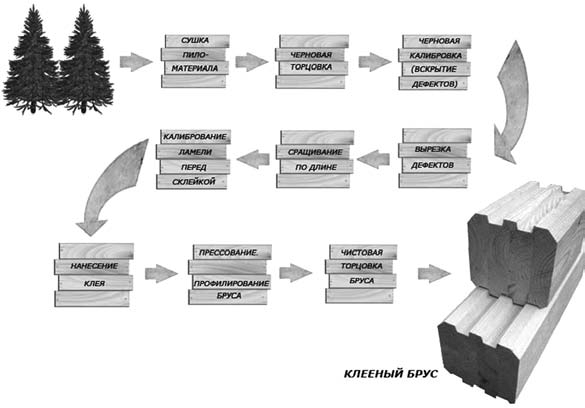
Рис. 31 Схема технологического процесса изготовления клееных деревянных конструкций
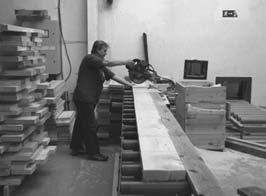
Рис. 32 Поперечный раскрой пиломатериалов на торцовочном станке
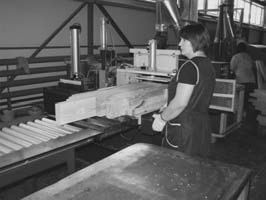
Рис. 33 Торцовка и вырезка дефектных мест
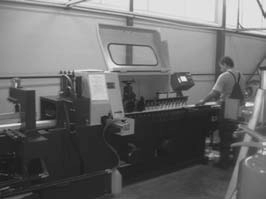
Рис. 34 Склеивание заготовок по длине на линии сращивания
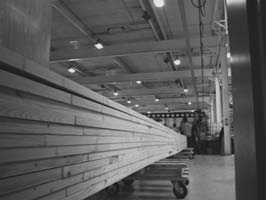
Рис. 35 Фрезерование ламелей с четырех сторон
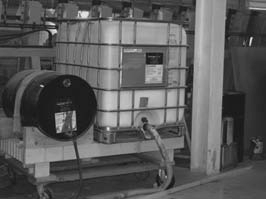
Рис. 36 Нанесение клея на поверхность ламелей на четырехстороннем строгальном станке
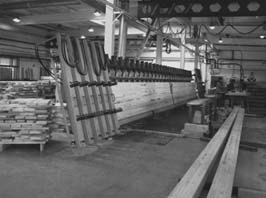
Рис. 37 Склеивание заготовок на гидравлическом вертикальном прессе
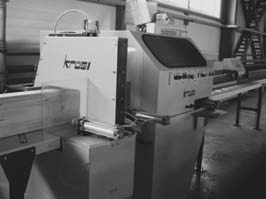
Рис. 38 Фрезерование профиля заготовки на четырехстороннем строгальном станке
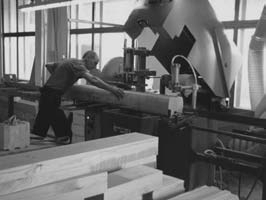
Рис. 39 Чистовая обрезка в размер
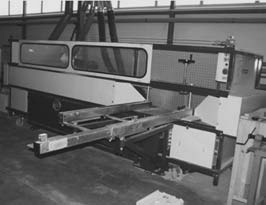
Рис. 40 Выпиливание углов
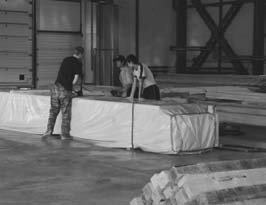
Рис. 41 Упаковка деталей клееного бруса
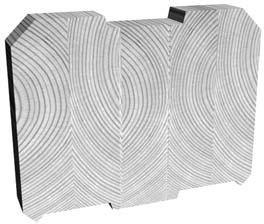
Рис. 42 Схема сборки ламелей клееного бруса «вразбежку»
При изготовлении клееного бруса необходимо учитывать возможность появления коробления в процессе эксплуатации. Для уменьшения вероятности коробления клееного бруса в процессе эксплуатации сборка заготовок должна производиться таким образом, чтобы направления волокон в смежных ламелях не совпадали (рис. 42).
Просмотров: 1 075
Соединение досок между собой
При изготовлении каких-либо столярный изделий нередко бывают моменты, когда длины доски не хватает. Как назло, вместо одной длинной есть несколько коротких. Опытные столяры в этом случае не бегут в магазин или на пилораму, а наращивают тесины по длине. Восстановленные изделия используются не во всех случаях. Например, для сидений на лавочках или для пола их лучше не применять, а для полотна двери или для стропил соединённые тесины вполне пригодны.
За долгие годы работы человека с деревом появилось множество способов соединения досок между собой. Один из таких приёмов мы рассмотрим в этой статье.
Итак, у нас есть 3 тесины, которые нужно соединить между собой в длину. Здесь надо отметить, что чем меньше отрезков используется для сращивания, тем прочнее окажется соединённый массив. В нашем случае получилось так, что для изготовления полотна двери не хватило одной дощечки. Поэтому пришлось её состыковывать из трёх коротких обрезков. Разумеется, части дощечек для сращивания должны быть равной ширины.
Первым делом разметим тесины. Соединим их в полдоски, то есть отрежем половину ширины от одного отрезка, половину — от другого. Часть одной тесины будет заходить на другую. Длины 10-15 см для выреза будет вполне достаточно, но чем больше это расстояние, тем прочнее будет соединение. Тут важно учитывать, что при разметке отрезков нужно помнить про ту длину, на которую планируется вырез. Например, если вы хотите сделать соединённую дощечку длиной 200 см, то общая длина двух отрезков должна быть больше на то расстояние, на которое планируется делать вырез. При вырезе 15 см длина двух досок составит 215 см. На 15-тисантиметровое расстояние одна часть тесины зайдёт в другую, и общая длина будет 200 см.
Таким же образов сделаем вырез на 2 и 3 отрезках.
Теперь дощечки нужно скрепить между собой. Мы для этих целей будем использовать мебельные шканты. На двух отрезках сделаем метки друг на против друга и просверлим отверстия глубиной, равной половине шканта. В отверстия капнем мебельного клея и забьём шкант, чтобы он торчал наполовину. В отверстия на второй дощечке тоже капнем клея и соединим отрезки между собой. Двух шкантов для соединения будет вполне достаточно.
Точно так же состыкуем и третью часть тесины.
Дальше увеличим прочность соединённого массива на изгиб. Для этого нам понадобится ручной фрезер.
Установим на него пазовую фрезу диаметром 2 см и настроим глубину реза, равную чуть больше половины толщины дощечки. Здесь главное не прорезать доски насквозь. Фрезером делаем по два паза с каждой стороны, захватив все 3 срощенные доски. Всего сделаем 4 паза, длина каждого – около 15 см.
В эти пазы вставим деревянные бруски, вырезав их из остатков тесины. Получается что-то типа шпонок, только эти шпонки удерживают два бруска в одной плоскости. Бруски должны заходить в пазы с усилием, чтобы они не двигались. Пазы намажем столярным клеем, вставим шпонки и забьём их молотком до упора. Высота брусков здесь не важна.
Лишние части брусков состругаем рубанком.
Чтобы шпонки не выскочили из пазов в случае высыхания дощечки, просверлим в них сквозные отверстия, вставим мебельные шканты и забьем их на всю толщину тесины. Выпирающие части шкантов снова состругаем рубанком.
На этом этапе соединение досок между собой завершено. Дальше начинаются отделочные работы, чтобы убрать зазоры, если это необходимо. Возьмём универсальную шпатлёвку и резиновым шпателем заполним щели.
Через пару часов, когда шпатлёвка полностью высохнет, отшлифуем тесину шлифовальной машинкой. Вот теперь соединённая дощечка готова к эксплуатации.
В нашем случае она была вставлена в дверное полотно. После изготовления двери и её покраски стало совсем незаметно, что доска состоит из нескольких частей. И на прочности двери это никаким образом не сказывается.
ВИДЕО
Сплачивание | Способы соединения древесины
Модели, стержневые ящики и другие части модельных комплектов, как правило, изготовляют не из целого куска древесины, а из отдельных кусков. Основными видами соединений частей древесных заготовок в модельном производстве являются сплачивание, вязка и частично сращивание.
Сплачиванием называется соединение досок или брусков по ширине и толщине, при котором долевые волокна древесины располагаются параллельно. Сплачивание применяют главным образом для получения щитов и массивных заготовок. При сплачивании целых заготовок из отдельных частей применяют клей, гвозди, шурупы, нагели, а сплачивание разъемных заготовок выполняют на шинах, клиньях и т. д. Наиболее распространенным способом сплачивания является соединение склеиванием встык пластями или кромками (рис. 92, а, б). Чем уже сплачиваемые доски (делянки), тем меньше будет коробление.
При сплачивании учитывают расположение годичных слоев древесины. Заготовки, выполненные сплачиванием встык пластями, достаточно прочные и почти не деформируются по сравнению с заготовками, соединенными кромками. Для наиболее ответственных работ применяют сплачивание пластями по способу, указанному на рис. 92, в. Выстроганная доска распиливается на бруски определенной ширины и пластями сплачивается в целую заготовку, но этот способ сплачивания значительно дороже способов, указанных на рис. 92, а, б.
Доски для разъемных моделей сплачивают так, чтобы годичные кольца были направлены выпуклой стороной к плоскости разъема (рис. 92,г), а для разъемных стержневых ящиков небольших размеров — наоборот (рис. 92, д).
Рис. 92. Примеры сплачивания:
а — встык пластями, б — встык кромками, в — встык пластями брусков распиленной доски (делянками), г — для разъемной модели, д — для разъемного стержневого ящика, е — в фалец, ж — в шпунт, з — на круглых шипах, и — в шпунт на рейку
Сплачивание может выполняться соединением досок и брусков в фалец (рис. 92,е) и в шпунт (рис. 92,ж), но эти способы сплачивания не обеспечивают плотного шва. Их применяют при изготовлении изделий без склеивания, работающих в условиях значительного изменения влажности.
При изготовлении широких и длинных щитов, чтобы повысить их прочность, в кромках досок ставят не менее двух круглых (рис. 92, з) или прямоугольных деревянных шипов на клею. Диаметр или толщина каждого из них должны быть равны 1/3 толщины щита, а высота — двойной толщине. Расстояние между ними до 500 мм устанавливать целесообразно в шахматном порядке. Разметку гнезд для шипов делают точно, шипы подгоняют плотно по гнездам, глубина которых должна быть больше длины шипов на 3—5 мм.
Сплачивание в шпунт на рейку (рис. 92, и) — один из несложных и удобных способов соединения досок кромками. Вставная на клею рейка обеспечивает прочность, а также точность сплачиваемых досок, так как кромки можно хорошо пристрогать друг к другу. Этот способ сплачивания экономичнее сплачивания в фалец и в шпунт, так как на рейку, изготовляемую обычно из отходов, не тратят часть доски.
Чтобы увеличить прочность и предупредить поперечное коробление, щиты скрепляют шпонками и наконечниками. Шпонка — деревянный брусок трапециевидной формы в поперечном сечении, который пригоняют к поверхности щита.
При изготовлении модельных комплектов широко применяют накладные шпонки (рис. 93,а). Шпонки плотно пригоняют к плоскости щита и приклеивают. Когда клеевой слой высохнет, ввинчивают шурупы. Этот способ простой, надежный и самый распространенный.
Склеивание щита шпонками в паз приводится на рис. 93, б в двух вариантах. По первому варианту шпонка 1 вгоняется в виде клина в сквозной паз, прорезанный поперек щита (может быть не сквозной), имеющий глубину, равную 1/4 толщины щита и суживающийся по длине к одному концу на угол 2—3°. Паз пропиливают награтной пилкой, подрезанный слой сначала скалывают стамеской, а затем зачищают зензубелем или грунтубелем. По второму варианту шпонку 2 изготовляют с заплечиками. Выступающая часть ее имеет одинаковую ширину по всей длине. Вгоняют такие шпонки в паз щита с клеем. Этот способ применяют для более ответственных частей модели и стержневых ящиков.
Пример скрепления щитка наконечником, насаживаемым шпунтом на гребень, сделанный на торце щита, показан на рис. 93, в. Чтобы крепление было прочнее, наконечник прикрепляют к торцу щита одним, иногда двумя скрытыми шурупами.
На рис. 93, г показан способ скрепления щита наконечником 3 в накладку с применением клея и шурупов. С другой стороны щит скреплен рейкой 4, которая на клею вгоняется в паз, сделанный в торце щита. Этим способом скрепляют толстые щиты. Толщина рейки 4 должна равняться примерно 0,4—0,5 толщины щита. Паз для рейки удобно выполнить на фрезерном станке.
Существует также способ скрепления ящиков рамкой в обвязку. Обвязка рамкой считается лучшей мерой предохранения щита от коробления. В столярном производстве ту часть щита, которая расположена внутри рамки, называют филенкой, а в целом щит с рамкой — филенчатым (рис. 93, д). Для укрепления щита в рамке на внутренних кромках брусков рамки делают шпунты или фальцы, а у щита соответственно гребни или фальцы.
В модельном производстве щит с обвязкой делают не сплошным, а сборным из отдельных досок, а между концами досок закладывают пробочные (пенопластовые) прокладки толщиной 1—2 мм, чтобы в случае повышенной влажности щит не порвал рамку и не покоробился.
Рис. 93. Скрепление щитов при сплачивании:
а — накладными шпонками, б — врезными шпонками, в — наконечником с шпунтом, г — наконечником внакладку и рейкой в шпунт, д — филенчатый щит; 1 — шпонка в паз, 2 — шпонка в паз с заплечиками, 3 — наконечник, 4 — рейка, 5 — филенка, 6 — рамка
Правила склеивания мебельного щита
Блок хаус
Часто спрашивают:
Вагонка
Порода дерева
Часто спрашивают:
Доска
Часто спрашивают:
Имитация бруса
Крепеж и саморезы
Крепёжный элемент
Часто спрашивают:
Мебельный щит
Наличник и плинтус
Напольные покрытия
Часто спрашивают:
Перегородки
Часто спрашивают
Обсадная коробка
Полок
Часто спрашивают:
Сайдинг
Производитель
Терраса дерево и ДПК
Часто спрашивают
Фальшбалки
Часто спрашивают: