Ферма (конструкция) — Вики
Ферма ж/д моста, используемая в конструкции антенны АДУ-1000.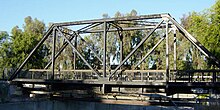
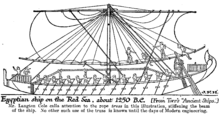
Фе́рма (фр. ferme, от лат. firmus ‘прочный’) — стержневая система в строительной механике, остающаяся геометрически неизменяемой после замены её жёстких узлов шарнирными. В элементах фермы, при отсутствии расцентровки стержней и внеузловой нагрузки, возникают только усилия растяжения-сжатия. Фермы образуются из прямолинейных стержней, соединённых в узлах[1] в геометрически неизменяемую систему, к которой нагрузка прикладывается только в узлах
К фермам с оговоркой можно отнести шпренгельные балки, представляющие собой комбинацию двух- или трёхпролётной неразрезной балки и подпружной тяги; они характерны для стальных и деревянных конструкций, с верхним поясом из неразрезного прокатного профиля (пиленые брусья или пакеты клееных досок). Также могут быть шпренгельные железобетонные фермы небольших пролётов.
Этимология
Слово «ферма» происходит от фр. ferme, которое в свою очередь восходит к лат. firmus (прочный).
Англоязычный эквивалент (англ. truss) происходит от старого французского слова фр. trousse, примерно от 1200 года н. э., что означает «вещи, собранные вместе»[3][4]
Область применения
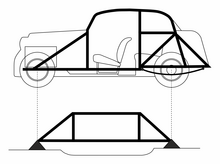
Фермы широко используются в современном строительстве, в основном для перекрытия больших пролётов с целью уменьшения расхода применяемых материалов и облегчения конструкций, например — в строительных большепролётных конструкциях, типа мостов, стропильных систем промышленных зданий, спортивных сооружений, а также при возведении небольших лёгких строительных и декоративных конструкций: павильонов, сценических конструкций, тентов и подиумов;
Фюзеляж самолёта, корпус корабля, несущий кузов автомобиля (кроме открытых кузовов, работающих как простая балка), автобуса или тепловоза, вагонная рама со шпренгелем — с точки зрения сопромата являются фермами (даже если у них отсутствует как таковой каркас — ферменную конструкцию в этом случае образуют подкрепляющие обшивку выштамповки и усилители), соответственно, в их расчётах на прочность применяются соответствующие методики
История
В 1844 году Д. И. Журавский начал изучать свойства мостов с решётчатыми фермами системы Гау по поручению П. П. Мельникова[11], а в 1856 году разработал свою теорию расчёта раскосных ферм и первый указал на существование скалывающих напряжений при изгибе.
В 1893 году
Ферменные конструкции МКС — Википедия
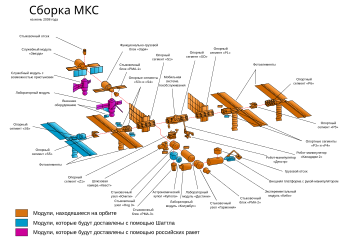
Ферменные конструкции
Широкое использование ферменных конструкций при космическом строительстве было запланировано в первоначальном американском проекте станции «Фридом» (англ. Freedom), который позднее, объединившись с российским проектом «Мир-2» и европейским «Колумб» (англ. Columbus), стал основой будущей международной станции. Согласно ранним планам НАСА, на орбиту должны были выводится детали металлоконструкций, из которых астронавты должны были бы собирать сами фермы, прямо в открытом космосе. Однако несмотря на определённые выгоды такого решения, для того чтобы удержать проект МКС во временных рамках в условиях нестабильного финансирования и снизить вероятность нештатных ситуаций, было принято решение доставлять на орбиту предварительно собранные элементы ферменных конструкций, которые бы легко монтировались экипажем шаттла.
Z1[править | править код]
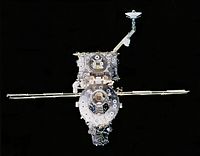
Конструкция фермы включает два плазменных разрядника, снимающих электростатический заряд, возникающий от трения станции об атмосферу, два модуля преобразователей постоянного тока, четыре гироскопа CMG (Control Moment Gyro), служащих для стабилизации станции, часть линии коммуникационной системы S-диапазона, коммуникационную систему Ku-диапазона, первичный и вторичный распределители энергии, оборудование системы термического контроля, механическое крепление для дальнейшего развития ITS, и роботизированное оборудование для выполнения внекорабельной деятельности.
P6[править | править код]
«P6» (англ. P6 Truss) — вторая ферменная конструкция запущенная к МКС после «Z1». представляет собой энергетический модуль с двумя солнечными батареями, длиной 36,58 метра каждая. Кроме этого внутри фермы смонтировано различное электротехническое и электронное оборудование, необходимое для преобразования, распределения и передачи полученной электроэнергии. «P6» была доставлена на станцию шаттлом «Индевор» (сборочная миссия МКС 4А, миссия шаттла STS-97) и 3 декабря 2000 года была установлена во временную позицию на ферме «Z1». Установка этой конструкции стала важным этапом для энергообеспечения научной программы станции и функционирования американского сегмента. В дальнейшем ферму «P6» предполагается перенести на постоянную позицию в левой части ITS.
S0[править | править код]
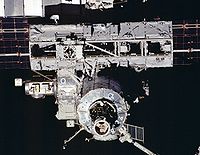
«S0» (англ. S0 Truss, полное название Center Integrated Truss Assembly (ITS) Starbord 0 (S-Zero) Truss) — ферменная конструкция длиной 13,4 метров и шириной 4,6 метра. Ферма весит 13,971 килограмм и в настоящее время служит центральной конструкционной основой ITS. Она была присоединена к лабораторному модулю «Дестини» в ходе сборочной миссии МКС 8A (миссия шаттла STS-110) 11 апреля 2002 года. Кроме своего структурного предназначения, как основного конструктивного элемента ITS, ферма «S0» также выполняет соединительную функцию между герметичными модулями МКС и внешними устройствами расположенными на ITS. Через кабели и трубопроводы размещённые на «S0» передаётся электроэнергия, данные, видеосигнал, а также аммиак для активной системы температурного контроля (
Масса: 13971 кг (30800 фунтов)
S1[править | править код]
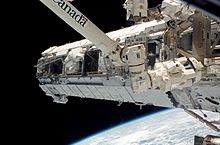
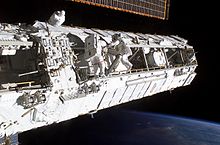
«S1» (англ. S1 Truss, полное название Starboard Side Thermal Radiator Truss) — ферменная конструкция присоединённая к правому борту фермы «S0» 10 октября 2002 года (шаттл «Атлантис», сборочная миссия МКС 9A, миссия шаттла STS-112). На ферме размещены рельсовые пути для тележки «Канадарма-2» и робокара (Crew and Equipment Translation Aid cart), предназначенного для перемещения экипажа и оборудования в ходе внекорабельной деятельности. Кроме этого в конструкции размещены радиаторы и другое оборудование для активной системы температурного контроля ATCS, в контурах охлаждения используется аммиак. Роторная радиаторная стойка поворачивает три радиатора на угол 105°, чтобы обеспечивать их постоянное нахождение в тени, а также подводит к ним электроэнергию и аммиак. На ферме размещены камеры и осветительные приборы, оборудование и антенны для системы связи S-диапазона.
Габариты: 13,7 x 4,6 x 1,8 метра (45 x 15 x 6 фута)
Масса: 14124 кг (31137 фунтов)
P1[править | править код]
«P1» (англ. P1 Truss, полное название Port Side Thermal Radiator Truss) — ферменная конструкция размещённая на левом борту центрального сегмента «S0». По своему устройству и предназначению является почти зеркальной копией фермы «S1». Смонтирована 26 ноября 2002 года экипажем шаттла «Индевор» (сборочная миссия МКС 11А, миссия шаттла STS-113). Кроме оборудования для связи в S-диапазоне, на «P1» размещена ещё и коммуникационная система в диапазоне ультравысоких частот (УВЧ, англ. UHF).
Габариты: 13,7 x 4,6 x 1,8 метра (45 x 15 x 6 фута)
Масса: 14003 кг (30871 фунтов)
P3/P4[править | править код]
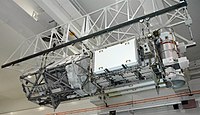
«P3/P4» (англ. P3/P4 Trusses) — ферменные конструкции, являющиеся продолжением развития левого сегмента ITS, присоединены к ферме «P1» и выполняют функции аналогичные фермам «S3» и «S4». Масса — 17,5 тонн. Конструкции были запущены 9 сентября 2006 года, на борту шаттла «Атлантис» в первой, после катастрофы «Колумбии», сборочной миссии (STS-115, ISS-12A). Монтаж был произведён с 11 сентября по 12 сентября 2006 года.
P5[править | править код]
«P5» (англ. P5 Truss) — небольшой сегмент, служащий для удлинения фермы «P6», был запущен на борту шаттла «Дискавери» (миссия STS-116) 7 декабря 2006 года и 12 декабря присоединён к ферме «P4», в ходе выхода астронавты также заменили неисправную камеру на сегменте «S1». Его необходимость обусловлена ограничением длины грузового отсека шаттлов и он состоит из самой фермы и кабельно-трубопроводных переходников.
S3/S4[править | править код]
«S3/S4» (англ. S3/S4 Trusses) — ферменные конструкции, являющиеся продолжением развития правого сегмента ITS, присоединены к левой ферме «S1» и служат для размещения двух солнечных батарей по 73 метра и 60 киловатт, а также радиатора и системы поворота. Фермы были запущены на борту шаттла «Атлантис», 8 июня 2007 года, в ходе полёта STS-117. 11 июня сегменты были успешно переданы манипулятором шаттла на «Канадарм-2», и подсоединены к ферме «S1». Установку затруднили проблемы с компьютерным оборудованием на российском сегменте станции, предположительно вызванные статическим током, возникшим при подключении нового сегмента.
S5/S6[править | править код]
«S5/S6» (англ. S5/S6 Trusses) — аналоги соответственно ферм «P5/P6», c установкой которых ITS полностью завершена, а энергоснабжение станции значительно увеличено, что позволяет проводить более энергозатратные научные исследования. Ферма «S5» была доставлена на МКС в ходе миссии «Индевор» STS-118. Сегмент, массой 1584 кг был размещён в грузовом отсеке шаттла, вместе с другой полезной нагрузкой. 11 августа 2007 года, в 21:45 (UTC) астронавты Ричард Мастрачио и Давид Уильямс начали монтаж фермы «S5».
15 марта 2009 года стартовала миссия «Дискавери» STS-119 с фермой «S6» на борту.[1] Эта ферма является последним крупным фрагментом МКС, который был поставлен Соединенными Штатами. «S6» имеет длину около 14 метров, масса всей конструкции 16 тонн и её стоимость составляет почти 300 миллионов долларов. 19 марта астронавты Смит Свэнсон и Ричард Арнольд вышли в открытый космос и осуществили монтаж сегмента «S6» ферменной конструкции.[2]
Ферма (конструкция) Википедия
Ферма ж/д моста, используемая в конструкции антенны АДУ-1000.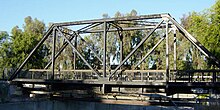
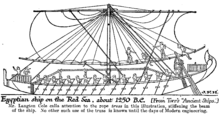
Фе́рма (фр. ferme, от лат. firmus ‘прочный’) — стержневая система в строительной механике, остающаяся геометрически неизменяемой после замены её жёстких узлов шарнирными. В элементах фермы, при отсутствии расцентровки стержней и внеузловой нагрузки, возникают только усилия растяжения-сжатия. Фермы образуются из прямолинейных стержней, соединённых в узлах[1] в геометрически неизменяемую систему, к которой нагрузка прикладывается только в узлах[2].
К фермам с оговоркой можно отнести шпренгельные балки, представляющие собой комбинацию двух- или трёхпролётной неразрезной балки и подпружной тяги; они характерны для стальных и деревянных конструкций, с верхним поясом из неразрезного прокатного профиля (пиленые брусья или пакеты клееных досок). Также могут быть шпренгельные железобетонные фермы небольших пролётов.
Этимология
Слово «ферма» происходит от фр. ferme, которое в свою очередь восходит к лат. firmus (прочный).
Англоязычный эквивалент (англ. truss) происходит от старого французского слова фр. trousse, примерно от 1200 года н. э., что означает «вещи, собранные вместе»[3][4]. Термин truss (ферма) часто используется для описания любой сборки элементов — таких, как псевдо-рамы[5][6] или пары стропил[7][8], часто означает инженерный смысл: «плоская рама из отдельных конструктивных элементов, соединённых концами в треугольники, для охвата большого расстояния»[9].
Область применения
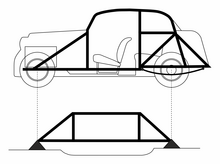
Фермы широко используются в современном строительстве, в основном для перекрытия больших пролётов с целью уменьшения расхода применяемых материалов и облегчения конструкций, например — в строительных большепролётных конструкциях, типа мостов, стропильных систем промышленных зданий, спортивных сооружений, а также при возведении небольших лёгких строительных и декоративных конструкций: павильонов, сценических конструкций, тентов и подиумов;
Фюзеляж самолёта, корпус корабля, несущий кузов автомобиля (кроме открытых кузовов, работающих как простая балка), автобуса или тепловоза, вагонная рама со шпренгелем — с точки зрения сопромата являются фермами (даже если у них отсутствует как таковой каркас — ферменную конструкцию в этом случае образуют подкрепляющие обшивку выштамповки и усилители), соответственно, в их расчётах на прочность применяются соответствующие методики[10].
Исто
Ферменная конструкция — Большая Энциклопедия Нефти и Газа, статья, страница 1
Ферменная конструкция
Cтраница 1
Ферменные конструкции состоят из отдельных стержней, воспринимающих в основном усилия растяжения или сжатия, сопровождаемые в некоторых случаях продольным или поперечным изгибом. Пояса и стержни ферм обычно представляют собой прокатные или сварные профили различных сечений. [1]
Опорная ферменная конструкция, изготовленная из боралю-миниевых труб, применена в стартовой конструкции, используемой при запуске спутников Земли, осуществляемом рекетой Атлас. Конструкция из труб, соединенных оловянно-серебряным припоем с алюминиевыми фитингами, имеет высоту 2 м, длину и ширину 0 8 м и на 51 % легче конструкции, изготовленной из алюминия. [2]
Ферменная конструкция произвольной геометрии ( возможно криволинейная) совместно с прилегающим грунтовым массивом рассматривается как единый объект, схематизируемый плоской системой прямых стержней с конечным числом инженерных ( переносных) степеней свободы. Полагается, что стержневая система обладает плоскостью материальной симметрии, совмещенной с главной плоскостью изгиба, в которой действуют нагрузки. [3]
Рассматриваемая ферменная конструкция составлена из рдинаковых изоляторов и поясов жесткости. Поэтому полученное значение Рв; представляет собой сосредоточенную ветровую нагрузку, приложенную к поясу жесткости, расположенному как между первым и вторым ярусами, так и между вторым и третьим ярусами. [4]
Дефекты ферменных конструкций по времени своего возникновения появляются при более позднем периоде эксплуатации. Наибольшее число дефектов наблюдается после 20 лет эксплуатации крана. [5]
Для сварных ферменных конструкций характерны повреждения в виде обрыва элементов или трещин в нижнем поясе в местах приварки раскосов горизонтальной фермы. Трещины и разрушения наиболее часто возникают в стыковых соединениях нижних поясов и узлах опорных раскосов. [6]
Для сварных ферменных конструкций характерны повреждения в виде обрыва элементов, трещин в нижнем поясе в местах приварки раскосов горизонтальной фермы. [7]
Рассмотрим элемент ферменной конструкции в виде прямолинейного стержня. Стержни равномерно нагреты, на систему действуют сосредоточенные силы, приложенные в узлах. Будем считать, что основное напряженно-деформированное состояние стержня достаточно точно описывается однородным растяжением-сжатием вдоль его продольной оси. [8]
Выделим в ферменной конструкции несущие и промежуточные слои. [10]
Стыки растянутых поясов ферменных конструкций, составленные из уголков или других прокатных профилей, в кранах режимов 4К — 8К, а также независимо от их режимов работы, но эксплуатируемых при температуре ниже — 20 С, должны быть выполнены соединением встык без накладок с разделкой кромок в соответствии с толщиной последних и с контролируемым полным проваром. [11]
При наличии в ферменной конструкции п ярусов она 8п раз статически неопределима. Поэтому точные методы расчета подобных конструкций затруднительны. Обычно для расчета их пользуются упрощенной инженерной методикой, рассмотренной ниже. [13]
В случае расчета сложной многоузловой ферменной конструкции, содержащей много дисков, изложенный выше подход, конечно, так лее применим, но он трудоемок. [14]
Страницы: 1 2 3 4 5
Ферменные конструкции МКС — это… Что такое Ферменные конструкции МКС?
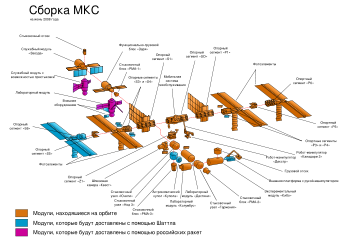
Ферменные конструкции — это одна из новых технологий, использованных НАСА при строительстве Международной космической станции. Фермы, доставляемые на орбиту шаттлом, монтируются его экипажем и служат для негерметичного хранения грузов, установки радиаторов, солнечных батарей, различного оборудования. Ферменные конструкции на МКС образуют так называемую ITS (англ. Integrated Truss Structure, Объединённая ферменная структура).
Широкое использование ферменных конструкций при космическом строительстве было запланировано в первоначальном американском проекте станции «Фридом» (англ. Freedom), который позднее, объединившись с российским проектом «Мир-2» и европейским «Колумб» (англ. Columbus), стал основой будущей международной станции. Согласно ранним планам НАСА, на орбиту должны были выводится детали металлоконструкций, из которых астронавты должны были бы собирать сами фермы, прямо в открытом космосе. Однако несмотря на определённые выгоды такого решения, для того чтобы удержать проект МКС во временных рамках в условиях шаткого финансирования и снизить вероятность нештатных ситуаций, было принято решение доставлять на орбиту предварительно собранные элементы ферменных конструкций, которые бы легко монтировались экипажем шаттла.
Элементы
Z1
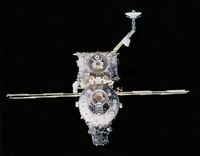
«Z1» (англ. Z1 Truss) — ферменная конструкция, смонтированная экипажем шаттла «Дискавери» в ходе сборочной миссии МКС 3A (миссия шаттла STS-92), сейчас не являющаяся основным элементом ITS, и служившая на ранних этапах сборки Международной космической станции временной площадкой для размещения фермы «P6» и элементом крепления американских солнечных батарей, установленных на модуле «Юнити» во время полёта шаттла «Индевор» (STS-97), для обеспечения энергетических потребностей станции.
Конструкция фермы включает два плазменных разрядника, снимающих электростатический заряд, возникающий от трения станции об атмосферу, два модуля преобразователей постоянного тока, четыре гироскопа CMG (Control Moment Gyro), служащих для стабилизации станции, часть линии коммуникационной системы S-диапазона, коммуникационную систему Ku-диапазона, первичный и вторичный распределители энергии, оборудование системы термического контроля, механическое крепление для дальнейшего развития ITS, и роботизированное оборудование для выполнения внекорабельной деятельности.
Коммуникационная система S-диапазона ITS состоит из двух избыточных линий, каждая из которых содержит по три заменяемых на орбите модуля и по две антенны, а также сигнальный процессор основного диапазона, транспондер системы слежения и ретрансляции данных и ещё одну группу антенн радиодиапазона, состоящую из двух направленных антенн с малым и высоким усилением.
P6
«P6» (англ. P6 Truss) — вторая ферменная конструкция запущенная к МКС после «Z1». представляет собой энергетический модуль с двумя солнечными батареями, длиной 36,58 метра каждая. Кроме этого внутри фермы смонтировано различное электротехническое и электронное оборудование, необходимое для преобразования, распределения и передачи полученной электроэнергии. «P6» была доставлена на станцию шаттлом «Индевор» (сборочная миссия МКС 4А, миссия шаттла STS-97) и 3 декабря 2000 года была установлена во временную позицию на ферме «Z1». Установка этой конструкции стала важным этапом для энергообеспечения научной программы станции и функционирования американского сегмента. В дальнейшем ферму «P6» предполагается перенести на постоянную позицию в левой части ITS.
S0
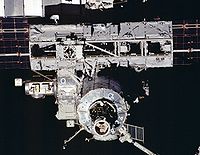
«S0» (англ. S0 Truss, полное название Center Integrated Truss Assembly (ITS) Starbord 0 (S-Zero) Truss) — ферменная конструкция длиной 13,4 метров и шириной 4,6 метра. Ферма весит 13,971 килограмм и в настоящее время служит центральной конструкционной основой ITS. Она была присоединена к лабораторному модулю «Дестини» в ходе сборочной миссии МКС 8A (миссия шаттла STS-110) 11 апреля 2002 года. Кроме своего структурного предназначения, как основного конструктивного элемента ITS, ферма «S0» также выполняет соединительную функцию между герметичными модулями МКС и внешними устройствами расположенными на ITS. Через кабели и трубопроводы размещённые на «S0» передаётся электроэнергия, данные, видеосигнал, а также аммиак для активной системы температурного контроля (Active Thermal Control System). Ферма также служит креплением для различного электронного оборудования, такого как устройства переключения основной шины, четыре преобразователя напряжения постоянного тока и четыре сборки распределителей вторичной энергии. Кроме этого на ферме смонтированы четыре антенны спутниковой навигации GPS и два гироскопа.
Тыльную сторону (со стороны американского сегмента станции) ферменной конструкции «S0» занимает 6,4-метровая панель радиатора, который рассеивает тепло выделяемое контейнерами с электроникой. На лицевой стороне «S0» и ещё десяти ферм размещены рельсы для Mobile Transporter — подвижной тележки, перемещающей главную «руку» станции, канадский манипулятор «Канадарм-2», вдоль всей длины Объединённой ферменной структуры (ITS). Габариты: 13,4 x 4,6 метра (44 x 15 фута)
Масса: 13971 кг (30800 фунтов)
S1
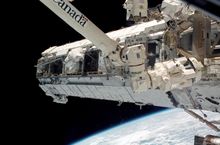
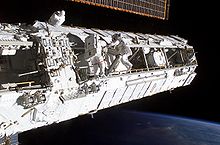
«S1» (англ. S1 Truss, полное название Starboard Side Thermal Radiator Truss) — ферменная конструкция присоединённая к правому борту фермы «S0» 10 октября 2002 года (шаттл «Атлантис», сборочная миссия МКС 9A, миссия шаттла STS-112). На ферме размещены рельсовые пути для тележки «Канадарма-2» и робокара (Crew and Equipment Translation Aid cart), предназначенного для перемещения экипажа и оборудования в ходе внекорабельной деятельности. Кроме этого в конструкции размещены радиаторы и другое оборудование для активной системы температурного контроля ATCS, в контурах охлаждения используется аммиак. Роторная радиаторная стойка поворачивает три радиатора на угол 105°, чтобы обеспечивать их постоянное нахождение в тени, а также подводит к ним электроэнергию и аммиак. На ферме размещены камеры и осветительные приборы, оборудование и антенны для системы связи S-диапазона. Габариты: 13,7 x 4,6 x 1,8 метра (45 x 15 x 6 фута)
Масса: 14124 кг (31137 фунтов)
P1
«P1» (англ. P1 Truss, полное название Port Side Thermal Radiator Truss) — ферменная конструкция размещённая на левом борту центрального сегмента «S0». По своему устройству и предназначению является почти зеркальной копией фермы «S1». Смонтирована 26 ноября 2002 года экипажем шаттла «Индевор» (сборочная миссия МКС 11А, миссия шаттла STS-113). Кроме оборудования для связи в S-диапазоне, на «P1» размещена ещё и коммуникационная система в диапазоне ультравысоких частот (УВЧ, англ. UHF). Габариты: 13,7 x 4,6 x 1,8 метра (45 x 15 x 6 фута)
Масса: 14003 кг (30871 фунтов)
S3/S4
«S3/S4» (англ. S3/S4 Trusses) — ферменные конструкции, являющиеся продолжением развития правого сегмента ITS, будут присоединены к левой ферме «S1» и служить для размещения двух солнечных батарей по 73 метра и 60 киловатт, а также радиатора и системы поворота. Фермы были запущены на борту шаттла «Атлантис», 8 июня 2007 года, в ходе полёта STS-117. 11 июня сегменты были успешно переданы манипулятором шаттла на «Канадарм-2», и подсоединены к ферме «S1». Установку затруднили проблемы с компьютерным оборудованием на российском сегменте станции, предположительно вызванные статическим током, возникшим при подключении нового сегмента.
P3/P4
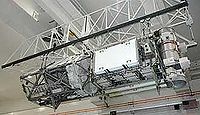
«P3/P4» (англ. P3/P4 Trusses) — ферменные конструкции, являющиеся продолжением развития левого сегмента ITS, присоединены к ферме «P1» и выполняют функции аналогичные фермам «S3» и «S4». Масса — 17,5 тонн. Конструкции были запущены 9 сентября 2006 года, на борту шаттла «Атлантис» в первой, после катастрофы «Колумбии», сборочной миссии (STS-115, ISS-12A). Монтаж был произведён с 11 сентября по 12 сентября 2006 года.
P5
«P5» (англ. P5 Truss) — небольшой сегмент, служащий для удлинения фермы «P6», был запущен на борту шаттла «Дискавери» (миссия STS-116) 7 декабря 2006 года и 12 декабря присоединён к ферме «P4», в ходе выхода астронавты также заменили неисправную камеру на сегменте «S1». Его необходимость обусловлена ограничением длины грузового отсека шаттлов и он состоит из самой фермы и кабельно-трубопроводных переходников.
S5/S6
«S5/S6» (англ. S5/S6 Trusses) — аналоги соответственно ферм «P5/P6», c установкой которых ITS будет полностью завершена, а энергоснабжение станции будет значительно увеличено, что позволит проводить более энергозатратные научные исследования. Ферма «S5» была доставлена на МКС в ходе миссии «Индевор» STS-118. Сегмент, массой 1584 кг был размещён в грузовом отсеке шаттла, вместе с другой полезной нагрузкой. 11 августа 2007 года, в 21:45 (UTC) астронавты Ричард Мастрачио и Давид Уильямс начали монтаж фермы «S5».
15 марта 2009 года стартовала миссия «Дискавери» STS-119 с фермой «S6» на борту.[1] Эта ферма является последним крупным фрагментом МКС, который был поставлен Соединенными Штатами. «S6» имеет длину около 14 метров, масса всей конструкции 16 тонн и её стоимость составляет почти в 300 миллионов долларов. 19 марта астронавты Смит Свэнсон и Ричард Арнольд вышли в открытый космос и осуществили монтаж сегмента «S6» ферменной конструкции.[2]
Примечания
Обсуждение:Ферма (конструкция) — Википедия
Материал из Википедии — свободной энциклопедии
Мне кажется, что подобный стиль не имеет права на существование. Возьмите любой учебник по строительной механике для начала — и вперед. Масса фактических ошибок, изложенных в весьма вольном стиле. —Petern 20:40, 27 мая 2010 (UTC)
Это бессмысленная фраза: «То есть, разбивают силы, действующие не в узлах, на соответствующие им пары сил»? —Petern 20:40, 27 мая 2010 (UTC)
«Однако, в расчётах этим традиционно пренебрегают и считают, что более жёсткое соединение элементов фермы создаёт запас прочности.» — Это КАТЕГОРИЧЕСКИ неверно. При наличии жестких узлов возникают изгибающие моменты, что НЕ идет в запас прочности. На самом деле принятие гипотезы о шарнирных узлах основано на большой гибкости стальных тонкостенных стержней и, соответственно, малых моментах, которыми пренебрегают. Для жб ферм эта гипотеза, конечно, несправедлива. Но в докомпьютерную и малокомпьютерную эпоху шарнирные узлы позволяли избежать трудоемкого расчета многократно статически неопределимой системы. Гипотеза о шарнирных узлах НЕ идет в запас прочности. Автор неправ. —Petern 20:40, 27 мая 2010 (UTC)
- Если Вам интересно, можете поправить.—1101001 17:18, 29 мая 2010 (UTC)
«Ферма состоит из элементов: пояс, стойка, раскос, шпренгель (опорный раскос).» Шпренгель не является опорным раскосом. Шпренгель в ферме — элемент, уменьшающий расчетную длину опорного раскоса, самый ненагруженный стержень системы. Опорный раскос — наоборот — самый нагруженный из раскосов, передающий нагрузки фермы и её вес на колонну. —89.189.142.14 17:27, 27 мая 2012 (UTC)
Что такое «веревочная ферма», которую автор обнаружил на египетском корабле? Сочетание «веревочная ферма» встречается в интернете только в одном месте — на этой странице википедии. Нет такой конструкции. Ферма в конструкции египетского корабля использовалась, но не таким образом. —Shperkh (обс.) 02:59, 2 августа 2018 (UTC)
Ферменные конструкции в качестве каркаса под оборудование. — КиберПедия
Сборка сухих отсеков.
Сборка сухих отсеков происходит в вертикальном положении в стапеле. Стапель – специальное приспособление внутри которого располагаются детали и узлы (сборки) стапеля для базирования, фиксации и сборки деталей отсека. Внутри стапеля части отсека устанавливаются на свои места (базируются), фиксируются, затем соединяются между собой (заклепок, винтов, шайб, гаек). Стапель состоит из нижней и верхней плит, на которые устанавливаются стыковочные шпангоуты. Сами плиты крепятся к колоннам. Между плитами располагаются детали и узлы (сборки) стапеля для базирования, фиксации и сборки деталей отсека.
Сборку ГО в стапеле производят в горизонтальном положении, собирая по отдельности каждую створку ГО.
Сборку сухих отсеков производит бригада рабочих, располагающихся на специальных рабочих площадках снаружи и внутри стапеля. Детали сухого отсека в основном соединяют с помощью заклепок, т.к. они значительно более легкие чем винты, шайбы, гайки. Винты применяют в тех местах сухого отсека, где значительные нагрузки. Клепку производят вручную специальным пневмоинструментом.
Сборку сухих отсеков в стапеле производят двумя методами:
1) с базой от каркаса – когда сначала в стапеле устанавливаются детали каркаса (стрингеры, шпангоуты, соединительные детали), они соединяются между собой, а затем устанавливают обшивку и соединяют ее с каркасом.
2) с базой от обшивки – когда сначала в стапеле устанавливают обшивку, а затем детали силового набора (каркаса), которые соединяются между собой и с обшивкой.
При любом методе сборки в стрингерах, шпангоутах, соединительных деталях уже имеются ведущие отверстия под крепеж. Эти отверстия при сборке рассверливаются до большего диаметра совместно с обшивкой и в них затем устанавливают заклепки и винты.
Стыковочные отверстия в стыковочных шпангоутах отсека сверлят в стапеле по отверстиям в нижней и верхней плитам стапеля, где эти отверстия уже имеются. Плазово-шаблонный метод обеспечивает взаимозаменяемость и точность как при изготовлении деталей отсека, так и при изготовлении и сборки стапеля. Это, в том числе, обеспечивает точное совпадение стыковочных отверстий в смежных отсеках при сборке ступени РН или при сборке целиком РН или КА.
Возможны два варианта сборки сухих отсеков в стапеле:
а) панелированная сборка – когда часть обшивки клепается со стрингерами (панель) вне стапеля, а затем устанавливается в стапель и собирается с остальными деталями сухого отсека,
б) непанелированная сборка – когда сборка сухого отсека от начала до конца идет только в стапеле.
Панелированная сборка считается более прогрессивной, т.к. вне стапеля можно клепать не вручную, а на прессе, что быстрее и качественнее. Кроме того, вне стапеля больше свободного места и одновременно клепать можно несколько панелей, а в стапеле в это время выполняются другие сборочные роботы. Таким образом, время сборки отсека сокращается.
После завершения сборки в стапеле отсек вынимается из него. Стыковочные шпангоуты фрезеруются по стыковочной плоскости, с них снимается небольшой припуск, в результате плоскости стыковочных шпангоутов параллельны с высокой точностью.
Снаружи сухого отсека по местам стыков деталей, по головкам крепежных деталей (заклепки, винты) наносят герметик, что обеспечивает пылевлагозащиту отсека. Герметик наносят полосами, перед нанесением на отсек эмали.
18.Изготовление и сборка ферменных отсеков РН и КА. Монтажные работы при сборке сухих и ферменных отсеков РН и КА.
Ферменные отсеки (фермы), так же как и сухие отсеки, негерметичны и соединяют другие отсеки между собой или крепят двигательную установку к корпусу ступени РН или к КА, но не имеют обшивки.
Ферма, чаще всего, состоит из двух стыковочных шпангоутов, между которыми располагаются прямолинейные стойки (тяги), соединяющие эти шпангоуты. Стыковочные шпангоуты служат для стыковки фермы со смежными отсеками РН или КА. На стыковочных шпангоутах находятся стыковочные отверстия под болты и штыри.
Для крепления стоек между собой и со шпангоутами служат соединительные детали – кронштейны, фитинги и другие. Две соседние стойки фермы и часть шпангоута между ними должны образовывать треугольник (треугольная форма является наиболее жесткой и устойчивой).
Ферма может быть без стыковочных шпангоутов, т.е. состоять из стоек и фитингов, соединяющих стойки. Основания фитингов образуют стыковочные площадки для соединения со смежными отсеками, на которых расположены стыковочные отверстия для болтов.
Детали силового набора фермы бывают трех типов:
1) стыковочные шпангоуты,
2) прямолинейные стойки (играют роли стрингеров и шпангоутов),
3) соединительные детали – кронштейны и фитинги.
По массе конструкции ферма легче аналогичного по размерам и назначению сухого отсека из того же материала. Ферма применяется тогда, когда не требуется наличие обшивки или обшивка специально не устанавливается.
Ферменный отсек используется при горячем разделении ступеней РН. В свободное пространство между стойками фермы выходит наружу дым и пламя в первые секунды горячего разделения ступеней. Если не обеспечить такой свободный выход для дыма и пламени, то можно повредить хвостовой отсек «новой» ступени РН или вызвать взрыв остатков ракетного топлива в отделяемой ступени РН.
Так же ферма используется при креплении ракетного двигателя к ступени (ферма и двигатель находятся внутри сухого отсека).
Еще одно применение ферменного отсека – промежуточный отсек между КА и последней ступенью РН, или между КА и РБ. Такой промежуточный отсек часто называют адаптер. С его помощью КА устанавливается на РН, а затем после выведения КА на околоземную орбиту КА отделяется от него (полное отделение от РН). Обшивка для такого отсека не нужна, т.к. отсек и КА находятся под ГО и не соприкасаются с атмосферой. Такой же промежуточный ферменный отсек используется и в том случае, если одна РН сразу выводит в космос несколько КА, расположенных на ферме параллельно.
Ферменная конструкция также применяется в качестве основы (корпуса) для посадочных блоков межпланетных КА. Часть такой фермы используется в качестве посадочных опор, а к оставшейся части фермы крепятся двигательная установка, топливные баки, приборы, оборудование и коммуникации различных систем межпланетного КА. Такой ферменный корпус применялся на посадочной части американского корабля «Аполлон» при пилотируемых полетах на Луну.
Особенностями ферменных отсеков являются:
1) высокая прочность и жесткость,
2) способность воспринимать ударные нагрузки (например, посадка на планету),
3) относительная простота конструкции,
4) высокая надежность,
5) относительно невысокая стоимость,
6) возможность точного изготовления несложными методами.
Основные требования к ферменным отсекам:
1) необходимые прочность и жесткость,
2) точность посадочных поверхностей – на стыковочных шпангоутах,
3) устойчивость стержневых элементов – не деформируются и не ломаются,
4) надежность соединения всех элементов (шпангоуты, стойки, соединительные детали) с помощью сварки или крепежных деталей,
5) точная центровка (положение центра масс) относительно продольной оси РН или КА,
6) требования, связанные с конкретным назначением фермы.
Материалом для изготовления деталей ферменного отсека служат, в первую очередь, различные алюминиевые сплавы. Реже в качестве материалов применяют титановые сплавы, высокопрочные стали, композиционные неметаллические материалы.
Схема изготовления ферм:
а) изготовление стоек из стандартных профилей или труб,
б) изготовление стыковочных шпангоутов из стандартных профилей,
в) изготовление соединительных деталей (фитингов и кронштейнов) из заготовок на металлорежущих станках,
г) сборка ферменного отсека в стапеле,
д) покрытие, контроль, маркировка, клеймение.
Схема изготовления стоек из стандартных профилей и труб:
1) резка профилей или труб по нужной длине,
2) слесарная зачистка заусенцев и притупление острых кромок,
3) обработка местных усложнений формы стойки для обеспечения сборки с соединительными деталями,
4) покрытие, контроль, маркировка, клеймение.
Схема изготовления стыковочных шпангоутов из стандартных профилей:
1) резка профилей по нужной длине, стыковочный шпангоут фермы делается из нескольких частей,
2) слесарная зачистка заусенцев и притупление острых кромок,
3) обработка местных усложнений формы шпангоута для обеспечения сборки с соединительными деталями,
4) гибка шпангоута в соответствии с формой ферменного отсека,
5) нанесение покрытия, контроль, маркировка, клеймение.
Заготовками для фитингов и кронштейнов являются поковки или отливки. Форма фитингов и кронштейнов довольно сложная, поэтому обработка производится на фрезерных станках, позволяющих обрабатывать эти плоскости. Часто применяют фрезерные станки с ЧПУ. Станки с ЧПУ обеспечивают более высокое качество обработки. После завершения обработки на станке проводится контроль, маркировка, клеймение, нанесение покрытия.
Более мелкие соединительные детали возможно изготавливать из листовых заготовок штамповкой.
Крепежные детали (винты, шайбы, гайки) изготавливаются в соответствии со стандартами для этих деталей или закупаются уже готовые на других предприятиях, входящих в кооперацию по изготовлению РН или КА.
После изготовления деталей приступают к сборке фермы. Сборку производят в вертикальном положении в стапеле, аналогично сухим отсекам.
После разделки стыковочных отверстий по шпангоутам фермы, ее вынимают из стапеля и фрезеруют стыковочные поверхности шпангоутов, снимая заранее предусмотренный небольшой припуск. Этим достигается параллельность стыковочных плоскостей шпангоутов фермы.
Для собранной фермы проводят контроль, маркировку, клеймение, нанесение покрытия и отправляют ее в цех окончательной сборки.
Соединение деталей фермы между собой возможно не только с помощью крепежных деталей, а и с помощью сварки. Возможно соединение деталей комбинированным способом. В случае применения сварки необходимо учитывать, что сварка нагревает соединяемые детали, в них возникают внутренние напряжения, которые могут вызвать деформацию сваренных деталей и всего ферменного отсека в целом. В таких случаях говорят, что детали и отсек «коробит» или «повело». Эти деформации будут тем больше, чем тоньше сваренные детали.
Чтобы снизить до приемлемых эти вредные последствия сварки, сварку деталей фермы ведут в определенном порядке, обеспечивающем минимальные напряжения и деформации в сваренной ферме. После сварки предусматривают отжиг (ТО) для снятия внутренних напряжений. В случае сборки фермы с помощью сварки проводят контроль качества сварных швов.
«+»: сварных соединений в облегчении конструкции.
«-» :сварной фермы – внутренние напряжения и деформации после сварки.
Классификация испытаний.
Все многообразие испытаний объединяется в систему испытаний, в которой есть определенные требования (правила), рассмотренные выше, а также существуют классификация и конкретные виды испытаний.
Испытания классифицируют по следующим признакам:
а) По месту проведения испытания могут быть наземными и летными (натурными). Промежуточное положение занимают так называемые огневые испытания. Они типичны для испытаний двигательных установок или отдельных ступеней РН. Наземные испытания могут быть заводскими, полигонными (в монтажно-испытательном корпусе космодрома) и предстартовыми, которые проводятся на изделии, установленном на стартовом столе.
б) В зависимости от уровня сборки испытуемого объекта испытания могут быть узловыми (сборочных единиц — узлов), агрегатными (отсеков, агрегатов, блоков) и общими (собранных РН или КА):
· Автономные испытания имеют целью проверку отдельных приборов или групп приборов, входящих в сборочную единицу, агрегат или изделие, на специальных стендах с заменой (имитацией) остальной части сборочной единицы эталонными приборами.
· Комплексные испытания собранных агрегатов и изделий имеют целью проверку входящих в них приборов на взаимодействие.
в) Исследовательские испытания проводятся с целью определения возможности реализации конструкторских идей в новом изделии.
г) Контрольно-технологические испытания имеют главной целью проверку на отсутствие производственных дефектов у серийных, устанавливаемых на летные образцы, узлов, агрегатов, а также полностью собранных летных образцов изделий.
д) Имитационными принято считать такие испытания, в которых создаются специальные уникальные условия космического пространства (вакуум, тепловое воздействие, излучения, невесомость и т.д.) в отдельности или в совокупности.
Виды испытаний.
При проведении испытаний отсеков РН и КА, их отдельных агрегатов, приборов и систем, а также при испытании целиком РН и КА, проводят следующие конкретные виды испытаний:
1) Испытания на функционирование отдельных систем, узлов, устройств и т.д. составляют основу большинства программ и методик. В чистом виде они представляют собой проверку работоспособности различных систем и устройств при отсутствии специально созданных внешних воздействий, т.е. при нормальных условиях цеха (при нулевом воздействии).
2) Испытания на статическую прочность состоят в определении фактических деформаций и напряжений в элементах и узлах аппарата при воздействии постоянных сил.
3) Испытания на герметичность — создание избыточных давлений или глубокого вакуума внутри или снаружи испытываемых емкостей (герметичные баки или жилые отсеки).
4) Динамические испытания — проверка функционирования конструкции, систем, механизмов и устройств изделия при воздействии на него разного рода динамических воздействий и снятие динамических характеристик изделия. В зависимости от характера и вида динамического воздействия различают отдельные виды динамических испытаний:
а) Вибрационные испытания — определяется способность элементов конструкции противостоять вибрационным нагрузкам, не разрушаясь и не получая механических повреждений, особенно опасно появление резонанса при колебаниях. Источником вибрации может служить ракетный двигатель и устройства двигательной установки.
б) Акустические испытания — разновидность вибрационных испытаний на звуковых частотах. Источниками акустических нагрузок в изделии являются шумы от истекающей огненной струи в ракетных двигателях, работы различных внутренних устройств, вибраций элементов КА на звуковой частоте и т.д. Акустические нагрузки воздействуют на элементы конструкции пока изделие еще двигается в атмосфере Земли, т.е. акустическая (звуковая) вибрация передается на конструкцию через воздух.
в) Ударные испытания имитируют ударные нагрузки, возникающие при разделении ступеней и отсеков, при раскрытии и сбросе створок головного обтекателя (ГО) РН, при раскрытии парашютной системы, при посадке аппарата, а также при транспортировке. При ударной нагрузке к конструкции изделии кратковременно прикладывается значительная сила, а затем в конструкции возникают колебания.
5) Температурные испытания бывают на теплоустойчивость или холодоустойчивость. Возможны испытания на циклический (повторный) нагрев (охлаждение) и на температурный удар (резкое изменение температуры).
6) Вакуумные испытания проводятся с целью определения функционирования различных систем, узлов и деталей в условиях вакуума, проверки герметичности, отсутствия холодного схватывания в подвижных соединениях изделия, скорости испарения материала.
7) Имитационные испытания на воздействие различного вида излучений (солнечное излучение, отраженное и собственное излучение Земли, космическая радиация) — испытывается радиационная стойкость материалов и воздействия излучений на различные элементы, приборы и оборудование.
8) Летные испытания проводятся с целью проверки аэродинамической формы изделия, эффективности теплозащитного покрытия, отражательной способности поверхности изделия, срабатывание парашютной и двигательной систем мягкой посадки.
Изготовление деталей баков.
Общая схема изготовления баков состоит из этапа изготовления отдельных деталей обеих групп и этапа сборки.
В подвесных баках обечайки имеют меньшую толщину, чем в несущих баках.
Длинные обечайки собираются обычно из отдельных цилиндрических секций (монолитных панелей), число которых может быть значительно, при их сборке одновременно устанавливаются и поперечные силовые элементы, кронштейны, перегородки и т.д., сборка производится в стапелях. Соединение с помощью сварки, которая обеспечивает герметичность. После контроля швов и приварки всех арматурных и установочных деталей обечайка поступает на сборку бака.
Стыковочные шпангоуты баков предназначены для стыковки обечаек с днищами баков и со смежными отсеками. К ним могут предъявляться более высокие требования по точности, герметичности, коррозионной стойкости.
Шпангоуты изготавливаются из стандартных профилей нужного поперечного сечения по обычной схеме изготовления.
По форме обводов днища, применяемые на РН и КА, могут быть сферическими, эллиптическими, параболическими, куполообразными и полуторовыми (половина тора) с бортами различной формы и без бортов.
По диаметру различают малогабаритные (до 300 мм), среднегабаритные (300-1000 мм) и крупногабаритные (более 1000 мм) днища. По составуисходных заготовок различают:
1) простые цельноформованные (штампованные),
2) сложные штампосварные конструкции днищ, сваренные из отдельных сегментов.
На технологию изготовления оказывают существенное влияние относительная толщина стенок (отношение толщины стенки к диаметру днища) и требуемая точность.
Для днищ в большинстве случаев используются листовые заготовки различной толщины (от 0,5 мм до 30 мм и выше). Основой изготовления днищ являются, как правило, методы холодного формообразования. Общие требования к днищам такие же, как и к бакам.
Обобщенная схема изготовления днищ:
1) Листы освобождают от упаковки, протирают смазку и осматривают поверхность: не допускаются царапины, вмятины, трещины и другие поверхностные дефекты; при необходимости производят контроль толщины.
2) Разметка очищенного листа производится с помощью разметочного инструмента, проверяется с помощью шаблона заготовки. Здесь же отрезаются образцы для механических испытаний и химического анализа; производится клеймение листов и образцов.
3) Раскрой заготовок днищ производится на гильотинных или роликовых ножницах, на фрезерных или карусельных станках, иногда газовой или плазменной резкой. Для сложных штампосварных днищ вырезаются треугольные или сегментные заготовки элементов днищ. Для крупных малонагруженных днищ могут применяться сварные (с последующей зачисткой и отжигом швов) листовые заготовки.
4) Если раскрой заготовки производится на ножницах или резкой, то контур ее обрабатывается механически. Кроме того, на этом этапе иногда производится механическая обработка (фрезерование на копировально-фрезерных станках) поверхности заготовок для получения вафельных или другой формы карманов с целью облегчения днища; иногда применяется для этого химическое фрезерование.
5) Заготовки после слесарной доработки тщательно протираются, обезжириваются и подвергаются отжигу (термообработка для снятия внутренних напряжений).
6) После отжига поверхности тщательно очищают, производят травление, промывку, сушку. Если операция формообразования производится со смазкой, то наносится соответствующая смазка.
7) В настоящее время известно много методов формообразования днищ: холодная листовая штамповка, обтяжка, ротационное выдавливание и обкатка, штамповка взрывом, вибрационная штамповка и другие.
Наибольшее распространение среди методов формообразования днищ находят методы листовой штамповки, наиболее освоенные производством: формовка, которая преимущественно выполняется за один переход и рекомендуется для днищ большой относительной толщины и малой относительной глубины; вытяжка различными способами. При изготовлении днищ из малопластичных материалов (магниевые и титановые сплавы) или из высокопрочных сталей с большой относительной толщиной применяют метод вытяжки с подогревом. Температура нагрева заготовки зависит от свойств материала. В некоторых случаях подогревается сам штамп. Применение штамповки с подогревом позволяет увеличить коэффициент и уменьшить число переходов при изготовлении днищ с большой относительной глубиной.
8) При многопереходном формообразовании днища подвергаются промежуточному отжигу. После операции формообразования днища или элементы сложных днищ проходят окончательную термообработку (отжиг, закалка, отпуск).
9) Формообразованные элементы сложных днищ после термообработки подвергаются механической обработке по кромкам под сварку на специальных кромкофрезерных станках.
10) После механической обработки производится слесарная доработка кромок, зачистка их, обезжиривание и подготовка под сварку.
11) Порядок сборки и сварки элементов днищ определяется их количеством и возможностью установки в одном приспособлении, которое должно обеспечить точное базирование элементов и возможность автоматической сварки по стыкам. После сварки производится отжиг сварных швов и контроль их методами неразрушающего контроля.
12) Сваренное днище поступает на операцию окончательной калибровки и правки. Элементы днищ до сварки проходят индивидуальную калибровку.
13) Для пробивки отверстий в днищах, число которых может быть значительно, применяют пробивные штампы.
14) При изготовлении крупных днищ их часто делают методом химического фрезерования. Эта операция может выполняться до формообразования или сразу после формообразования до сварки и вырубки отверстий.
15) Днища поступают на операцию нанесения покрытий (анодирование, кадмирование и т.д.), иногда наружная поверхность днищ шлифуется или полируется для получения высоких отражательных характеристик, например, чтобы отражать тепловые потоки, тогда покрытие не наносится (чистый металл).
После этого днища поступают на общую сборку бака в стапеле с помощью сварки.
22.Изготовление обечаек из монолитных панелей. Сборка герметичных отсеков. Система испытаний герметичных отсеков.
Монолитная панель – это одна единая деталь. Обечайка (боковая поверхность) герметичного отсека собирается сваркой из таких монолитных панелей. Монолитные панели включают в себя обшивку с продольным и поперечным набором (ребра жесткости). Эти ребра жесткости играют роль стрингеров и промежуточных шпангоутов, как у сухих отсеков, но только они входят в состав монолитной панели для обеспечения герметичности панели.
В монолитных панелях ребра жесткости могут быть или только в продольном или в продольном и поперечном направлениях («вафельного» типа), или расходящимися лучами из одной точки. Применение монолитных панелей вызвано, с одной стороны, постоянным увеличением нагрузок на конструкцию и стремлением в то же время сохранить их массовые характеристики, с другой стороны, развитием технологических методов изготовления монолитных панелей с достаточно тонкими ребрами и обшивкой, позволяющими реализовать этот массовый выигрыш.
Конструктивными преимуществами являются:
1) Меньшая масса при равной прочности
2) Уменьшение трудоемкости проектирования, конструкции за счет уменьшения количества элементов;
3) Увеличение прочности, жесткости, устойчивости за счет уменьшения числа стыков и швов, некоторое увеличение внутреннего объема агрегата,
4) Высокая герметичность конструкции,
5) Высокое качество наружных поверхностей обшивок.
Технологическими преимуществами монолитных панелей являются: уменьшение объема сборочных работ и во многих случаях суммарной механической обработки, уменьшение работ по герметизации, высвобождение производственных площадей и сборочного оборудования, упрощение сборочной оснастки, уменьшение стоимости изготовления панелей.
Недостатками монолитных панелей являются значительная стоимость заготовительной оснастки, низкий коэффициент использования металла, удлинение цикла подготовки и переналадки производства из-за длительности проектирования и изготовления оснастки. В опытном и единичном производстве применение монолитных панелей иногда может привести к удорожанию опытных изделий, технологические преимущества их полностью выявляются при серийном производстве.
Существует много способов изготовления монолитных панелей: механическое фрезерование из плит, прессование, прокатка, горячая штамповка, литье, химическое фрезерование, размерная электрохимическая обработка и другие. Применяют следующие методы изготовления монолитных панелей:
1) Механическое фрезерование монолитных панелей является одним из распространенных методов их изготовления, особенно в опытном и серийном производстве. Прямолинейные плоские панели фрезеруют из плит на копировально-фрезерных станках, позволяющих получать ребра жесткости любого расположения, и станках с программным управлением.
Панели криволинейной формы одинарной кривизны изготовляют из плит по двум схемам:
а) фрезерование плоской плиты, затем гибка ее по форме отсека,
б) гибка плоской плиты, а затем фрезерование криволинейной плиты.
Преимуществами механического фрезерования монолитных плит являются относительная простота оборудования, простота и дешевизна оснастки, возможность получения панелей различных конфигураций с любым расположением ребер жесткости и с любой толщиной, высокая точность и хорошее качество поверхности. Но такие недостатки, как низкий коэффициент использования металла (много стружки), большая трудоемкость и худшие механические характеристики металла панели, обусловили рекомендацию этого метода только для опытного и единичного производства. В серийном производстве этот метод допустим только в период подготовки более производительного метода.
2) Прессование монолитных панелей является одним из самых производительных способов их изготовления. При этом обеспечивается высокий коэффициент использования металла, более высокие механические свойства заготовок и высокое качество поверхности. Недостатком этого метода можно считать ограничения по форме и размерам панелей: можно получать панели только с продольными ребрами жесткости шириной до 850 мм и с толщиной обшивки не менее 2-3 мм. Для получения панелей с переменным по длине сечением применяется дополнительное фрезерование.
3)Прокатка монолитных панелей: преимуществами этого метода являются возможность получения панелей с толщиной обшивки менее одного миллиметра и панелей вафельного типа. Заготовками для панелей с продольными ребрами служат прессованные панели, которые в результате прокатки удлиняются за счет утонения обшивки и ребер. При прокатке панелей вафельного типа листовая заготовка — плита, сложенная с матрицей, имеющей обратную конфигурацию, прокатывается через гладкие валки, где металл заготовки перетекает в углубление матрицы. Посредством многократной прокатки с постепенным сближением валков получают вафельную панель требуемой формы. Процесс идет при температуре горячей штамповки. Технология обработки таких панелей и подготовки их к сборке в оболочки аналогична технологии изготовления прессованных панелей.
4)Горячая штамповка монолитных панелей на мощных прессах является методом, позволяющим получать панели с любой конфигурацией и переменной толщиной по длине ребер и со стыковыми узлами, что обеспечивает значительный выигрыш в массе и лучшую конструктивную прочность.
«-»: необходимость прессов большой мощности, длительный срок изготовления штампов, невозможность получения стенок малой толщины (менее 5-8 мм), низкая точность и достаточно сложная технология. Горячештампованные панели подвергаются длительной и сложной механической обработке или химическому фрезерованию. Объем такой обработки может быть уменьшен применением операции горячей калибровки. Горячештампованные панели рекомендуется применять в сильнонагруженных конструкциях при серийном, крупносерийном и массовом производстве.
5) Литье монолитных панелей
«+»: возможность получения панелей с различным расположением ребер, с более тонкой обшивкой, большая производительность, уменьшение объема механической обработки, уменьшение периода технологической подготовки производства, отсутствие больших усилий в процессе формообразования, возможность более быстрой переналадки оборудования.
«-»: худшие механические характеристики, они находят применение в малонагруженных агрегатах, когда их преимущества оказываются эффективными.
Метод литья панелей должен удовлетворять следующим условиям: до застывания металла в любом сечении через него должен пройти весь металл, питающий последующие сечения, и излишек металла из последующих сечений; при застывании не должно образовываться усадочных раковин, т.е. застывающие участки должны подпитываться жидким металлом; процесс литья должен обеспечивать удаление шлаков из отливки; желательно обеспечивать более плотную структуру металла в процессе литья. Методами, отвечающими этим условиям, является литье выжиманием, бесшовная заливка под низким давлением, центробежное литье.
6) Химическое фрезерование (размерное контурное травление) монолитных панелей
При химическом фрезеровании на металлический лист наносятся линии специальной мастики (краски). Там где наносят эту защитную краску будут ребра ячеек вафельной панели. Металлический лист опускают в ванну с раствором электролита. Под действием электрического тока в растворе электролита с непокрытых краской мест частицы металла уносятся и образуются углубления (ячейки) вафельной панели.
Преимуществом химического фрезерования по сравнению с механическим фрезерованием является при обеспечении высокой точности (до 0,05 мм) возможность получения панелей самых разнообразных форм и размеров с широкими и узкими пазами. При химическом фрезеровании исключаются деформации панелей. Метод позволяет создавать более равнопрочные конструкции. Химически фрезерованные панели практически не требуют дальнейшей ручной слесарной доработки и после отработки местных усложнений формы (отверстия, пазы и т.д.) передаются на сборку. При этом процессе прочностные показатели поверхностного слоя исходного материала не улучшаются из-за отсутствия поверхностного пластического деформирования (наклепа).
Сборка герметичных отсеков(аналогично сухим отсекам).
Испытания на герметичность.
Испытания на герметичность относятся к основным видам испытаний баков, обеспечивающих надежность и качество их в эксплуатации, проводятся для всех без исключения баков, после всех испытаний баков на прочность и динамических испытаний.
Герметичностью называют свойство бака не пропускать рабочий компонент (жидкость или газ) через соединения или через поры основного материала. Хотя герметичность связана с отсутствием утечек реального рабочего компонента, называемого рабочей средой, испытания обычно проводятся с помощью контрольных веществ (жидкостей или газов), называемых контрольными (пробными или индикаторными) средами. Контрольная среда обладает, как правило, большей проникающей способностью и меньшей стоимостью. Кроме экономических преимуществ это обеспечивает более высокую надежность испытаний, безопасность при испытаниях и меньшее влияние (например, коррозионное) на испытуемое изделие, что особенно важно для штатных (применяемых в летных изделиях) баков.
Герметичность характеризуется количественным параметром, называемым степенью герметичности, под которой понимается объемное или массовое количество вытекающего через места утечки компонента в единицу времени при определенных условиях. Допускаемая степень герметичности задается конструктором исходя из условий правильного функционирования и эксплуатации бака. Т.е. абсолютной (идеальной) герметичности не существует, всегда есть некоторые утечки компонента из конструкции, а с помощью степени герметичности устанавливаются приемлемые для конструкции бака утечки компонента.
При контроле герметичности важнейшей характеристикой метода и аппаратуры (схемы испытаний) является чувствительность. Чувствительность схемы испытаний должна быть выше, чем заданная (контролируемая) степень герметичности емкости. Чувствительность определяется с помощью контрольной течи — установки, с помощью которой создается поток контрольной среды заданной величины. Степень герметичности, определяемая в результате испытаний, должна быть меньше, чем заданная — в этом случае бак удовлетворяет требованиям конструкторской документации (чертежи, технические условия (ТУ) и другие) и считается годным.
Все методы испытаний герметичности можно разделить на две группы:
1) определение суммарной негерметичности, которая определяет степень герметичности бака в целом, не определяя места возможных утечек,
2) определение локальной негерметичности, связанное с определением конкретных мест утечек контрольной (или индикаторной) среды.
В ТУ могут задаваться степень как суммарной, так и локальной негерметичности по отдельным местам бака (сварные швы, места разъемных соединений и другие).
Значительно более высокой чувствительностью обладают методы определения негерметичности с помощью специальных течеискателей и индикаторных газов, которые основаны на определении наличия и концентрации определенного индикаторного газа в заданном объеме. Наиболее распространенными типами течеискателей являются масс-спектрометрические с использованием в качестве индикаторного газа гелия(гелиево-воздушная или азотно-гелиевая смеси). Преимуществами гелия как индикаторного газа являются малое содержание его в атмосфере (5.10-4%), высокая проникающая способность, химическая инертность, безвредность и взрывобезопасность, невоспламеняемость. Гелиевые течеискатели состоят из трех основных узлов:
1) ионного источника, в котором молекулы газа, сталкиваясь с электронами, ионизируются в ионы с положительным зарядом е;
2) анализаторной камеры, в которой ионы ускоряются под действием электрического поля и приобретают скорость, зависящую от их массы m, и разделяются под действием магнитного поля на компоненты в зависимости от отношения m/е и скорости;
3) коллектора с регистрирующим устройством, определяющим интенсивность выделенного ионного пучка данного газа.
Кроме этих основных узлов течеискатели имеют выносные пульты управления (ВПУ) с приборами-указателями и рабочий щуп для забора смеси газов в контролируемой точке, откачные системы с вакуумными насосами и устройствами для создания контрольной течи для калибровки течеискателей (эталоны).
Существует много различных конструкций течеискателей масспектрометрического типа с высок